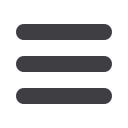

SAIW: Thermal spray coatings seminar
7
March 2015
AFRICAN FUSION
up to 300 to 800 m/s; and the modern
cold spray process, which, at tempera-
tures below300 °C, accelerates particles
towards a substrate at up to 1 000 m/s.
Each process type has its own niche in
the market.
“From left to right, we can see
these processes as first, second, third
and fourth generation thermal spray
developments. The higher the particle
velocity, the better the layer quality
and bond strengths. And the lower the
temperature can be kept, the less the
chance of oxidisation occurring while
a particle is travelling to the surface.
The combination of high velocity and
low temperature characteristics make
cold spray processes very attractive
for sensitive and expensive coatings,”
she adds.
In terms of the coatings themselves,
since substrate temperature can be
maintained below 200 °C with good
thermal management, there is no heat-
affected zone (HAZ) or dilution between
the substrate and coating. Due to the
mechanical bondand the layerednature
of the coating structure, the material
properties of the coating are not the
same as bulk cast/wrought coating ma-
terial properties would be. And while a
vast range of coating properties can be
achieved, it is generally not a good idea
to subject coatings to high point or line
impact loading.
“Components can be coated with
metals, alloys, carbides/cermets, oxides,
polymers, blends and graded coatings.
Deposition rates of between 1.0 and
20 kg/hr can be achieved and, with the
addition of the cold spray process, the
thickness range is almost unlimited –
from 20
m to > 30 mm.
“The greatest limitation is that it is
a line of sight process. If you have a thin
narrowborewith limitedaccess, it is very
difficult to coat the inside of it,” Lovelock
informs. She also advises caution in
some aqueous corrosive environments,
because “thermal spray coatings are not
generally recommended for corrosion
barrier protection in the as-sprayed
condition, because they do not seal.
While penetration could take years, the
coating itself cannot be guaranteed to
last forever, even if it has been success-
fully subjected to laboratory corrosion
tests and appears to be fully dense. This
does not apply to sacrificial corrosion
protection coatings, however, because
this protection does not depend on a
sealed barrier,” she explains.
Overview of thermal spray
coating technologies
Flame spray processes
Powder flame spray is a subsonic
flame-based process. Powder is blown
or drawn into an annular combustion
chamber where an aspirating gas and
a fuel gas are mixed and combusted,
creating a high velocity (subsonic) ex-
haust stream. A second outer annular
gas nozzle feeds a streamof compressed
air around the combustion flame, which
accelerates the spray particles towards
the substrate and focuses the flame.
The powder can be fed through a
small hopper on the gun, or via larger
freestanding powder feeders. There are
also several fuel gas options, depending
on the application and temperatures
required. “It is a low velocity, low tem-
perature process and, because the par-
ticles are projected through air, a surface
layer with relatively high proportions of
oxides, porosity and unmelted particles
is produced,” says Lovelock.
Wire flame spraying is a similar
process, except that the coating mate-
rial is fed into the flame spray gun as
solid wire. The flame melts the wire,
which is then atomised and accelerated
towards the substrate by the annular
compressed air flow. Also a subsonic
process, Lovelock says that the wire
feed rate and flame settings have to be
balanced toproduce continuousmelting
of thewire anda continuous spray of fine
particulate. Showing amicrograph of an
aluminium coated sample she points
out the black lines of oxide stringers
and says, “If you consider how easily
aluminiumoxidises, this is not too bad”.
The flame spray processes have low
capital and running costs. They can be
done on-site and by hand, if appropriate
safety precautions are adopted, and
they offer adequate surface properties
for low-stress build-up applications and
sacrificial coatings. “They are suitable
for non-demanding applications such as
repairing wear or corrosion damage on
non critical parts that are not intended
for demanding engineering applica-
tions. A variety of iron- and nickel-based
powders are available for repair and
salvage,” she adds.
Avariationof theseprocesses are the
spray and fuse processes, also known
as spray-brazing, which involve remelt-
ing the fused layer – with a flame, in a
furnace in by induction heating – after
it has been deposited. “The fusingmelts
and seals the surface and can produce
ametallurgical bondwith the substrate.
The process is commonly used to coat
glass formingplungers andglassmoulds
with a NiCrBSiFe alloy, a ‘self-fluxing’
alloy with low melting point. This coat-
ing is known to produce a favourable
surface interaction with molten glass
(silica) which at 700 °C is very abrasive,”
says Lovelock.
Arc wire spray
The key difference between these pro-
cesses and flame-based process is that
an electric arc is used to generate the
requiredheat. Themost commonly used
variation is twinwire arc spraying, where
a dc electric arc is struck between two
continuously fedwires. Thewire speeds
are set to balance the melt-off rate of
the wires and to keep the arc stable.
On melting, droplets are propelled by
compressed air or an inert gas jet onto
the surface being coated.
Arc spraying is a very high produc-
tivity thermal spraying process with de-
position rates for steel at 10 to 14 kg/hr
and up to 5.0 to 8.0 kg/hr for aluminium.
“With flame spray, it is possible to spray
unmelted powders onto a surface, but
with twin wire arc spray, the coating
material has to be melted before it is
sprayed,” Lovelock notes. The process is
simple to operate; canbe usedmanually
or automated and a wide range of met-
als, alloys andmetal matrix composites
(MMCs) can be deposited, including a
limited rangeof carbide-basedmaterials
that are available in cored-wire form.
Generally speaking, the coating
quality is better than flame sprayed
coatings, with less porosity, fewer ox-
ides and higher bond strengths. The
Void
Oxide inclusion
Unmelted particle
Substrate
Features of thermal spray coatings: “The bonding
mechanisms at the interface and between the coating
‘splats’ is still subject to some speculation, but while
both mechanical interlocking and diffusion bonding
may occur, mechanical bonding predominates,” says
Lovelock.
Image ©ASM International.