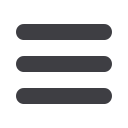

Eternal India
encyclopedia
ART
ENAMELLING
Enamelling as an art form was in-
troduced into India in the 16th century,
probably by the European goldsmiths
at the Mughal court. The main centres of this art have been Jaipur,
Varanasi, Lucknow and Pratapgarh.
The enamels used by the goldsmiths of India are limited to a
few shades of colours, one of the reasons being non-availability of
raw materials. Jewellery enamel colours are not produced in India.
Enamel in art is the coloured vitreous material fused by heat on
gold, silver or copper. The process requires three distinct, but
absolutely essential components, the metallic base, the enamel and
the oven.
The enamel itself is made up of silicon sand (upto 50 per cent),
sodium carbonate, potassium carbonate and lead mixed with me-
tallic oxides. Hundreds of different hues can be created by combin-
ing varying proportions of metal oxides. The combined ingredients,
after being melted in a furnace at a temperature of about 1400 °C for
approximately 15 hours, are poured like a batter on to cold iron
slabs. Then the enamel is allowed to harden into small cakes
which, when needed, are pounded into powder in a mortar. This
powder is rinsed several times before being used. Due to its
transparency and lack of colour, it resembles crystal, but it becomes
opaque with tin or titanium oxides, sodium fluoride or calcium phos-
phate.
Cobalt oxides are added to blue shades, manganese and cobalt
oxides to purples, tin oxide to whites, iron and uranium oxides to
yellows, copper oxides to reds and deep yellow etc. The powdered
enamel, either dry or mixed with water or oil to make a paste or
liquid is then applied to the metal surface. The enamel colours are
sorted out according to the manufacturer's numbers rather than by
the name of the colour. For example No. 478 refers to emerald
green (opaque), No. 120 refers to ultramarine blue (transparent)
and so on. Quite- often the result of the fused enamel colour is
different from the raw original enamel. It is not possible to mix
enamel as a pigment, like oil or water colours, as each colour of the
enamel retains its own distinct hue even after firing.
THREE TYPES
Enamels are opaque, translucent, opalescent and transparent.
Opaque enamels show no light, signs or metal through them as
Enamelled Haka
stand, of Mughal
period
translucent and opalescent materials do.
Transparent enamels naturally permit all ar-
eas and surface to be clearly seen. They can
be fired over opaque in successive firing to
give a rich, pool-like effect.
Enamels are classified into three types, soft, medium and hard
depending on the temperature required to melt them. Enamel fuse
at a temperature of approximately 700 to 730° C for soft, 730 to
770°C for medium and 770 to 820° C for hard types.
The firing
temperature and the firing time depends on various
factorssuch as
the thickness and the size of the metal, the quantity of objects
placed in the muffle, the thickness of the enamel layer, the type and
temperature of the kiln etc.
The techniques of applying enamel concern the treatment of the
metallic base. In fact, the base involved in the final aesthetic
aspect by making use of its natural colour. The techniques are
called Cloisonne, Champleve and Bassetaille or painting.
Cloisonne (partitioned) enamel is traditionally applied to gold
in the West and to bronze in the Orient. Metal bands or wires,
often gold or silver, are fixed to the surface of the base plate by
soldering so as to form a dividing line in the design. Enamel is
poured into these divided zones, obtaining a type of stained glass
or mosaic whose tesserae are circumscribed precisely by the metal
fillets. A layer of enamel is applied or deposited into cells and
heated until the enamel melts.
Champleve is another technique. The desired design is trans-
ferred to a copper (or silver or gold) plate of at least 2 mm
thickness. Using a burin, the area on the metal surface is removed
where enamel will be placed up to a depth of one mm. The border of
the wall is corrected to get a clear finish. The wells may also be
achieved by means of a particular engraving method, etching. In
this technique the parts of the design that will not be covered with
enamels are protected with a suitable bitumen varnish.
When the plate is dipped into acid, only the uncovered parts are
corroded, creating wells which can be refinished with a burin. Damp
enamels are applied to these zones using a spatula and the first
firing is done to be followed by others depending upon the required
result. The area where enamels have overflown may be removed
by rubbing them with a hard abrasive and water. Thereafter, one
more firing is done, often applying a little of colours, to get a good
result. This technique is called Champleve because it is obtained