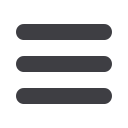

ART
Eternal India
encyclopedia
Here the stalls sold brasswork, incense burners, lamps, and many
other things concerned with ceremonial worship.
In Bengal Kanska plates were a speciality of Burdwan and
Midnapore. Several other places in Burdwan division were noted
for their metal pots and pans.
The brass work of Nagpur, consisting of lotas, kators, and cook-
ing vessels were distinguished by their pure traditional forms.
Brass and bell-metal vessels were manufactured at Sambalpur in
Orissa.
Nasik, Poona and Ahmedabad had always been famous for their
copper and brasswork. Iron work was also done at Ahmedabad.
There was a large manufacture of idols in all the metals at Nasik
and Poona.
gala. Magadi, Belur and Channapatna in Karnataka. Turmkur was
noted for its brass and copper utensils and idols. Nellore was
famous for its brass work. The finest brass work was done at
Madurai and Tanjore.
The temple bells of India were celebrated for the depth and
purity of their note and those of Madras are distinguished by their
stately architectural forms.
Damascened work
Damascening is the art of encrusting one metal on another in the
form of wire, which by undercutting and hammering was completely
incorporated with the metal which it was
intended to ornament.
It was limited to encrusting gold wire
and sometimes silver wire, on the sur-
face of iron, or steel, or bronze. It takes
its name from Damascus, where it was
carried to the highest perfection by the
early goldsmiths.
In India it was carried on chiefly in Kashmir, Gujarat and in the
Nizam's dominion. Damascening in silver was called bidri, from
Bidar, in the Nizam's dominion, where it was principally produced.
In bidri the metal ground is a compound of copper, lead and tin,
made black on the surface by dipping it in a solution of sal -
ammoniac, saltpetre, salt and blue vitriol. This alloy, after being
first melted and cast, was turned in a lathe to complete the form,
which was usually that of the ordinary sarai, or water goblet, or
hukah stand.
Bidri was also made in the Bhagalpur division of Bengal. Here
only zinc was mixed with copper in the alloy.
Arms
: Indian steel has been celebrated from the earliest antiquity
and the blades of Damascus, which maintained their pre-eminence
even after the blades of Toledo became celebrated, were in fact of
Indian steel. Twenty miles east of Nirmal and a few miles south of
the Shisha hills, occurs the hornblende slate or schist from which
the magnete iron used for ages in the manufacture of Damascus
steel, and by the Persians for their sword blades, was obtained. The
Dimdurti mines on the Godavari were also another source of
Damascus steel.
In the Punjab, superbly ornamented arms of the costliest de-
scription, were made at Lahore, Sialkot, Gujarat, Shahpur and in
Kashmir. Arms were also made at Monghyr. Swords of good
temper were made at Pehani, in the Hardroi district of Oudh.
Nagpur was noted for the manufacture of steel weapons, such
as spears and daggers. In Tumkur arms and cutlery were produced
for sale all over Mysore.
The most striking objects in the Prince of Wales collection of
Indian arms was a suit of armour made entirely of the horny scales
of the Indian armadillo or pangolin encrusted with gold, turquoises
and garnets.
There was another splendid suit of Kashmir chain armour.
The collection also includes the great sword of Mahmud Chand
Sultan Shah of the date of 1707 and the sword of the famous polygar
Kattabomman Naik who defeated the English in the early 19th C.
Pottery
Unglazed pottery has been made from before the time of Manu.
The principal varieties of Indian fancy pottery made for export were
the red earthernware pottery of Travancore and Hyderabad in the
Deccan, the red glazed pottery of Dinapur, the black and silver
pottery of Azimghar in North Western Provinces, and Surrujgurrah
in Bengal (Bhagalpur), imitation Bidri of Patna and Surat in Gujarat,
painted pottery of Kota in Rajputana, the glazed and unglazed
pottery of Madura and the glazed pottery of Sindh and the Punjab.
The Indian potter's wheel is of the simplest and crudest kind. It
is a horizontal fly-wheel, two or three feet in diameter, loaded
heavily with clay around the rim, and put in motion by the hand, and
once set spinning, it revolves for five or seven minutes with a
perfect steady and true motion. The clay to be moulded is heaped on
the centre of the wheel and the potter squats down on the ground
before it. A few powerful turns and the wheel spins silently, while
the shapeless heap of clay begins to grow under the potter's hand
into a perfect form; which is carried off to be dried and baked. Pol-
ishing is done by rubbing the baked jars and pots with a pebble.
There is a great demand for these clay pots, since the Hindus have
a religious prejudice against using an earthen vessel twice.
Sandalwood and other wood carvings
Sandalwood carving was chiefly carried out at Surat, Ahme-
dabad, Bombay, Canara, Karnataka and Travancore. The best
Canara carving came from Kumta and the best of Mysore, identical
with that of the Canara, was from the jtown of Sorab in Shimoga.
One beautiful example was a little cabinet exhibited by Major
Puckle in the Annual International Exhibition of 1871. It was
surmounted by a triangular headboard on which were carved
Brahma and Saraswati in the centre, and Shiva on Nandi on one
side, and Shiva and Vishnu coalesced in Krishna on the other, the
outline of this headpiece being waved in a manner to represent the
mystic trilateral monosyllable AUM . On either side of it was an
elephant waving a chauri in its trunk, and below it a narrow border
on which were carved Lakshmi, Parvati, Garuda, Hanuman and
other gods. On the right door of the cabinet Visnhu on Garuda, with
Lakshmi by his side, was represented in the centre, surrounded by
the forms of his ten avatars, and on the left door Shiva on Nandi,
with Parvati by his side, was represented in the centre surrounded
by the guardians of the eight quarters of the earth, Indra, Agni,
Yama, Nirritu, Varuna, Vayu, Kubera and Isana.
Brass and copper vessels were made at Madhugiri, Nagamn-