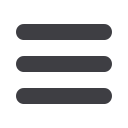

Eternal India
encyclopedia
HANDICRAFTS
The ancient culture of the country and its
rich diversity are reflected in the infinite
variety of its handicrafts. The skills of its
craftsmen have evolved over the centuries
shaped by the cultural influences and cross-
currents that have been generated by the
making of Indian history.
What is the real significance of handi-
crafts? It lies in the newness and surprise
of each object. No two are alike, for each is
a fresh creation. Standardisation is alien, in
‘fact a negation of all that handicrafts stand
for. Even the poorest enjoyed a variety in
the articles of everyday use, for a special
article was assigned for a particular use.
This meant a wide range even in the clay
water pots and pans, clothes and garments
with distinctive colours and designs. Wall
and floor decorations varied according to the
days of the week and to mark special festi-
vals. All this broke monotony which is per-
haps the most deadening element in life.
- Kamaladevi Chattopadhyay
HANDLOOM TEXTILES
India has been the source of fine cotton,
wool and silk textiles for centuries. Cotton
was first produced in India and fine cotton
cloth called muslin was in great demand in
the Roman Empire, and the other ancient
civilisations of Egypt and Babylonia. Dis-
tinctive styles of weaving developed in dif-
ferent parts of the country. Handlooms
have survived the process of industrialisa-
tion and today there are nearly 4 million
HANDICRAFTS
handlooms engaged in weaving cotton, silk
and other fabrics (including man-made
fibres) out of which 3.5 million weave cot-
ton. Nearly 10 million are employed in the
handloom sector. The export of handloom
products went up to Rs. 807 crores in 1989-
90 from Rs. 631 crores the previous year.
The popularity of the handloom fabrics
lies in their attractive colour schemes, de-
signs and craftsmanship. Although the
handlooms now use mill made yam and
chemical dyes, the use of handspun yarn and
vegetable dyes has not been forgotten alto-
gether. The looms have been modernised to
increase productivity. Yet it is the deft
human hands that have to weave the fabric
inch by inch. The entire process of weaving,
including dyeing, is done manually. The for-
tunes of the industry are closely linked with
that of the village. Each village in India
specialises in a different variety of fabric.
All the four types of natural silk — mul-
berry, tassar, muga and eri are produced in
India. While India stands fourth in the pro-
duction of mulberry raw silk, she has a mo-
nopoly in the production of
muga.
She is
also the second largest producer of tassar
silk. Sualkuchi in Assam is a famous centre
for silk weavers, which produces typical
Assam items like
mekhela,
a women's
lungi,
chaadar
and
riha.
Kashmir has become an important
centre for the lighter type of modern silk
fabrics like georgette, chiffon, ninon etc.
South India is known for its heavy qual-
ity silks. In Tamil Nadu Kanchipuram and
Kumbakonam are famous centres. Kan-
chipuram silk sarees with their rich gold
borders with traditional designs adopted for
modern wear have become very popular.
Karnataka is known for its silk sarees,
being one of the states in the country which
produces silk. Kollegal is a famous centre in
Karnataka. There are several varieties of
silk sarees— thick raw silk, soft Bangalore
silk, spun silk, crepe silk and georgettes.
Madhya
Pradesh
has
Maheswari
sarees, which are woven with fine cotton
and silk and have reversible borders which
can be worn either side and Chandiri sarees
in which silk as warp and fine cotton for the
weft in subtle shades are used.
The rich gold brocades of Banaras (Var-
anasi) are famous all over the world. The
best weavers are Muslims. The best known
brocades are the Belbar or scroll pattern
which appears in the Ajanta frescoes. An-
other is the Butidar or sprig design. All the
sarees have heavy gold borders or silver
background with gold patterns superim-
posed.
The Patola sarees of Patan (Gujarat)
are produced by the Ikat technique, a tie and
die weave resulting in identical patterns on
both sides of the fabric. Orissa has its own
Patola style done in tussar silk and in single
Ikat.
The cottons of Andhra Pradesh are
known for their fine quality. Gadwal and
Kothakota produce fine cotton sarees with
rich borders. Venkatagiri makes sarees
which are a sheer weave with gold coins,
dots, leaves, parrots or simple geometrical
patterns.
The plain white saree with a gold band
for border is typical of Kerala and is known
as Karalkuda.
Aurangabad, which was part of Hydera-
bad State till States' reorganisation in 1956,
is the home of Himroo. The style of weaving
is associated with the advent of Muslim rule
in India. It is Persian in origin. Himroo cloth
is an extra weft fabric with a solid coloured
background decorated with floral motifs.
The tradition of Himroo weaving has been
revived and kept alive in Hyderabad through
the efforts of Suraiya Hasan Bose.
The textiles of Manipur, Assam and
Tripura have near-geometric motifs sym-
bolising animals, birds, flowers and human
beings. The Orissa weaver is inspired by
temple carvings and weaves patterns of
fish, flowing streams, trees and flowers
using the Ikat technique.
In Rajasthan, the tying and dyeing of
woven fabrics, known as
Bandhani
, is a
technique representing the earliest form of
resist patternings. Parts of the fabric are
tied with thread into minute knots to form a
design and dipped into dye. The combination
of various colours with the base which is
dyed in a different shade produces innumer-
able variations in pattern.
But despite this regional distinction
there has been a great deal of exchange in
technique and styles. The Surat
tanchoi,
based on a technique of satin weaving with
the extra weft floats absorbed in the fabric
itself, can also be seen in Varanasi. The
Jamadani
technique — the patterns are
worked in white on a white background, the
extra weft threads which create the pattern