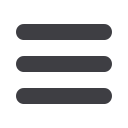

HANDICRAFTS
being of the same fineness as those used in
the fabric - was brought to West Bengal by
weavers who migrated from East Bengal
(now Bangladesh) and is used in weaving
Daccai saris. Varanasi craftsmen have also
borrowed the
Jamadani
technique.
Woollen fabrics are no less enchanting.
The famous Kashmiri shawl is made from
wool (
Pashmina
) from the underneck part of
a rare breed of Tibetan antelope. The shawl
is supposed to pass easily through a ring
but yet is warm enough to hatch a pigeon’s
egg-
The shawl industry in Kashmir received
an impetus from the Mughals. Akbar and
his successors wore Kashmiri shawls. Af-
ter Napoleon presented a rare shawl to Em-,
press Josephine France went crazy over
shawls.
Jannwar shawl is rare; threads of the
wrap and weft are dyed before weaving.
Special charm of this shawl is the harmoni-
ous blending of colour schemes depicting
architectural and mythological figures inter-
woven with landscape design.
Designs have to be worked evenly on
both sides to make the shawl attractive. A
good Pashmina shawl may cost a few
hundred to thousand rupees depending upon
the workmanship involved and time con-
sumed for its completion.
The major output in shawls today is of
the embroidered type with the base cloth
woven out of raffal - 40 and 60 counts wool-
len yarn. These handwoven shawls are em-
broidered with hand motifs.
HANDPRINTED TEXTILES
Printed textiles are fabrics on which a
pattern is produced after the cloth is woven.
There are different ways in which this can
be done.
1. The direct or application process —
known as block printing or screen print-
ing. The wooden block or silk screen is
applied directly on the fabric.
2.
The resist process — portions of the
cloth are covered with wax, clay, gum or
other resist so that when the cloth is
subsequently dyed the colour does not
penetrate these portions. Batik is a re-
sist process. In the
Bandhani
tech-
nique, the flow of colour is restricted by
tying certain portions of the fabric with
thread before dyeing. The weavers of
Andhra Pradesh and Orissa tie and dye
yarn in this way before weaving. The
patolas
of Patan are similarly treated.
3.
The mordant-madder, alizarin and indigo
process. The cloth is prepared with vari-
ous mordants so that when it is im-
mersed in a dye bath, the reaction pro-
duces different colours on the cloth. Only
the prepared portions take the dye.
4.
The discharge process. In the modern
process the cloth is first dyed in the
background colour with dischargeable
colours. The design pattern is then
printed on with chemicals which dis-
charge the background colour and fix the
colour which is printed along with the
chemicals. The design can then be fur-
ther processed.
5.
Application of thick pigment or
roghan
to
the fabric. This produces patterns which
appear to be encrusted on the fabric.
Hand printing is extensively done in Ra-
jasthan. Barmer has a special print called
Ajrakh, printed on both sides, which con-
sists of blue and red geometrical patterns.
This is used for turbans and shawls. In
Nathdwara printed sarees, wraps, large
kerchiefs and quilt covers are available.
Sandalwood blocks are used for printing.
This leaves a lingering scent in the folds of
the cloth. Jaisalmer in the border area of
Rajasthan has a special type of resist which
is done only in winter at night as it has to be
done at low temperatures.
In Gujarat there are several centres like
Jamnagar, Bhavnagar, Rajkot and Vasna
each with its own rich traditions. Kutch is
famous for satin prints called gajji. The col-
our is black and red with peacock, bird, ani-
mal and flower motifs.
In Uttar Pradesh Farrukhabad has tradi-
tional designs ranging from butis (dots) to
the Tree of Life. Mango "paisley" designs
are made in a variety of shapes. The tree of
life is a complex and intricate piece of work
with delicate details. A complete block con-
sists of anything from 1000 to 2000 pieces.
Lucknow is noted for its paisley designs.
Mathura's craft is rooted in religion and my-
thology with scenes and episodes from
Krishna's life.
Eternal India
encyclopedia
The Malva region of Madhya Pradesh is
renowned for its printed cottons. Important
centres are Bhairongarh, Jawad, Tarapur,
Umedpura and Sheopur. The large floor
covering, Jajam, has an impressive design,
the Neempatti, a large 24-petalled flower,
bounded by four neem leaves linked to-
gether by two four-petalled and two six-
petalled flowers arranged alternately. The
border has a flower and leaf motif running
like a creeper,
CARPETS AND OTHER
FLOOR COVERINGS
The Mughal emperor, Akbar, in the 16th
century, introduced the art of pile carpet
weaving in India when he brought Persian
carpet weavers to India and set up the royal
workshop in his own palace.
The Indian carpet industry began by imi-
tating the Persian in style and technique but
has gradually acquired a character of its
own. India produces carpets in several sizes
and varying lengths of pile from as low as 1/
4" as in Kashmiri carpets to 7/8" as in the
Indo-Berber carpets which are made from
handspun wool. In addition to designs from
Persia, Afghanistan, Turkey, China, Mo-
rocco and France, a number of distinctly In-
dian designs have evolved in recent years.
Of the Central Asian designs made in Ka-
shmir, the most outstanding is Bokhara in
which warp and weft are prepared in wool.
Imported wool blended with high-grade
Indian wool is used for superior quality car-
pets. The yarn used is mostly millspun. For
fine quality carpets, such as Kashmir car-
pets, worsted yarn is used. The best quali-
ties, made with high grade wool, develop a
lustre after use. However since there is a
demand for carpets with lustre even before
they are used, lustrous wool pile is used.
This is a process of chemical, washing which
enhances the natural lustre of the wool, the
fibre becoming smooth and shiny. But if the
washing is not carefully done, this could
reduce the life of a carpet.
The finest carpets come from Kashmir,
where a carpet has 400 knots per square
inch. But good carpets are also made in
Amritsar (Punjab), Agra (Uttar Pradesh),
Jaipur
(Rajasthan),
Gwalior
(Madhya
Pradesh), Warangal and Elluru (Andhra
Pradesh). Some Muslim families in Elluru
claim to be direct descendants of Persian
migrants. Carpet weaving was introduced
to Warangal by craftsmen who formed part
of the Mughal Army-.