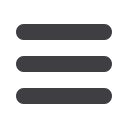

news
Wire & Cable ASIA – January/February 2009
30
Rigid cage stranding machine
Rigid cage stranders from Cortinovis Machinery can produce copper, aluminium or aluminium alloy conductors, from 7 to
91 wires in a single pass and up to 169 wires using a second pass. Strand constructions can be round, sector shaped,
straight or pre-spiralled, compressed or compacted, and be made from single round, trapezoidal or specially shaped wires.
The machines have the option of screening with bobbins of multi-wires or a single wire on each bobbin, and armouring with
steel wires. A full range of accessories is available for all products.
The process is fully controlled from a central PLC with a main operator interface and remote operator interface using
Profibus with a controlled stop in the case of power failure. Recipes, predictive maintenance and production reports are
included. The machine has automatic multiple loading and unloading of bobbins, using lifting platforms with side conveyors
or side trolleys. Different versions of compact design rigid stranding cage are available for bobbin diameters of 500, 560,
630, 710 and 800mm. Fail-safe safety devices lock the bobbin in the machine and provide unbalanced load detection and
alarm. The machines are designed for easy access for wire string up and welding.
The table shows working speeds, with
automatic tension control, from full to empty
bobbins. Wire material can cause variation.
Automatic re-charging of the air tank and
the bobbin braking circuit is carried out at
every loading operation, without intervention
of the operator; at the same time the pintles
pneumatic circuit is connected and allows
the loading/unloading of the bobbins.
The pneumatic pintles are actuated by air with a separate circuit from the bobbin braking system. The pintle locking is
fail-safe and is mechanically locked during rotation. An electrical interlock is also provided. A wire break detection system
checks for breaks in each individual wire, by monitoring the rotation of each bobbin; the control desk displays which bobbin
is involved and the machine automatically stops.
Wire tension is maintained by pneumatic disc brakes; the friction pads are
easily changeable. Tension is set up at the control desk and can be
changed while the machine is running.
Loading platform with rotating turntable
:
The cage is automatically positioned in the loading position. An
hydraulically-operated lifting platform is fitted in the floor. The platform
lifts and moves the full bobbins in between the open pintles. In each
sequence a full row of bobbins is loaded; the sequence is automatic
with safety interlock controls at all steps. As an option, the platform can
include rotating turntables that assist the operator in the positioning
of full bobbins.
Loading platform with conveyors
:
Chain conveyors, on which the operator puts all the full bobbins while
the machine is running, move a complete row of full bobbins onto the
lifting platform.
Using the side loading trolley
:
Side loading trolleys are installed on rails on the floor, and do not require foundations. All the bobbins are prepared in
position while the machine is running. The trolley automatically takes and lifts the bobbins, and places them between the
open pintles. Safety interlocks are in force at all steps.
Cortinovis Machinery – Italy Fax
: +39 035 313211
:
cortinovis@cortinovis.itWebsite
:
www.cortinovismachinery.comNumber of bobbins
speed up to
diameter 630mm standard DIN 46397 [rpm]
6 and 12 bobbin cage
320
320
18 bobbin cage
280
280
24 bobbin cage
265
230
30 bobbin cage
220
190
Rigid cage stranding machine from Cortinovis
m
m
Spanish steel maker Celsa Atlantic, a company of the Celsa
Group, has awarded a $5million contract for a second
compactor and coil handling extension to Siemens VAI in
order to increase productivity and improve product quality.
This represents the expansion of an existing system. Celsa
Atlantic expects delivery in the first quarter of 2009.
The coil handling extension includes a combination vertical
and horizontal system and a second compactor, and provides
increased on-line coil storage as well as an increase in surge
capacity. The greater cooling times will enable Celsa Atlantic
to produce higher quality products, such as thermo-
mechanically treated ribbed rebar for concrete reinforcement,
at its plant in La Coruña, Spain. The contract with Morgan
Construction, the US based specialist of Siemens VAI for high
speed wire rod mills, also includes a reloading station that
can route coils back into the system for offline processing.
Siemens VAI Metals Technologies GmbH & Co – Germany
Website
:
www.siemens.com/metalsCelsa Atlantic coil handling contract for Siemens