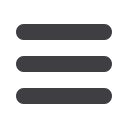

news
Wire & Cable ASIA – January/February 2009
33
New manufacturing concept for precision
micro flexible flat cables (FFC)
Flexible flat cables (FFCs) have found widespread use in the automotive and
IT industries. Lamination and extrusion are the processes most commonly used
for the production of FFCs but the disadvantage of lamination is its extremely low
production speed. Extrusion is unsuitable for the production of micro FFCs due
to the high temperatures and pressures encountered in the extruder head, and
these make it impossible to maintain accurate geometrical dimensions and
precise positioning.
Medek & Schoerner has
developed a new un-
pressurised cold process
for the production of FFCs
using UV cured resins, thus
ensuring the perfect geo-
metrical accuracy of the
cable at high production
speeds.
The procedure can also be
employed inline with an
extruder to position the indi-
vidual flat cables accurately
as they enter the extruder
head.
The same system, with some detail modification, also allows the coating of fine
steel wire in varying colours.
Medek & Schoerner GmbH – Austria Fax
: +43 1 982 72 96
:
m+s@medek.atWebsite
:
www.medek.atHigh-capacity wire rod mill
with FRS
®
technique
ArcelorMittal Hochfeld GmbH has placed an order with SMS Meer for the
supply of a complete high-capacity wire rod mill with FRS
®
technique for
high-grade steels. The annual capacity will be 690,000t. Of this, the major
portion of the products will be cold heading steel grades. The mill will be
designed for producing wire rod in high-grade steels and will go into
production in August 2010.
The SMS Meer order comprises a walking-beam furnace, the mechanical and
electrical equipment of the mill train, all of the supply systems, the finishing
facilities for the wire-rod coils, the entire rolling and cooling equipment, and
the erection and installation. The walking-beam furnace for billets up to
155mm square will reach an output of 120t/hour.
The wire rod outlet comprises a cooling and equalising section in a loop
arrangement, a six-stand wire rod block and a four-stand FRS
®
(Flexible
Reduction and Sizing) block – both in UHD (Ultra-Heavy Duty) arrangement.
The wire-rod block and the FRS
®
block are each followed by a water-cooling
line. The core component of the mill is the FRS
®
block together with the
cooling and equalising section. The supply scope therefore also includes the
104m long LCC
®
(Loop Cooling Conveyor) for forced and retarded cooling, a
total of three water cooling lines and the CCT
®
(Controlled Cooling Technology)
system developed by SMS Meer.
These facilities allow wire rod to be produced over the entire dimensional
range of 5.5mm to 25mm by means of temperature-controlled rolling.
Ultra-fine microstructures can be achieved especially for cold-heading grades
by thermomechanical rolling. The maximum rolling speed for 5.5mm wire rod
is 120m/sec.
SMS Meer GmbH – Germany
Fax
: +49 2161 350 1667
:
info@sms-meer.comWebsite
:
www.sms-meer.comFFC with 12 Cu conductors 0.035 x 0.600mm
m
m