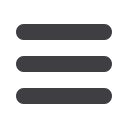

news
Wire & Cable ASIA – January/February 2009
32
The aluminium and copper market is continuously evolving. International aluminium customers are looking for improvements
while focusing their demand on special sizes to be applied to aluminium and copper production lines. During the past five
years the rod producers’ main interest has been in medium (8 T/h) and large (13 T/h) capacity rod lines. Properzi has
manufactured and installed lines of this type throughout the world, while extending its production range at the opposite
ends of the spectrum with an XS and an XXL line. Two years ago, during this wave of evolution and increased production,
Continuus-Properzi designed an aluminium line to produce approximately 1.6 T/h of grade rod in the standard diameter of
9.5mm. This small line was nicknamed the Properzi Baby line and its main components are shown in the diagram.
Giulio Properzi, president of Continuus-Properzi, is designing and developing XXL rod lines, to complete the range of
Properzi rod lines. These include an aluminium rod line for 20 T/h, a copper rod line for 45 T/h and an ingot casting machine
for 30 T/h. At present there are over 24 sizes and models of aluminium and copper rod lines in the Properzi repertoire,
ranging from XS up to XXL.
Continuus-Properzi SpA – Italy
Fax
: +39 02 98 10 358
:
sales@properzi.itWebsite
:
www.continuus-properzi.comNew drying system for wire and cable
Air Control Industries (ACI) has introduced a new energy-efficient drying unit for water-cooled, insulated cable and wire.
Called the ‘DRI-Line Powerpack’, ACI’s system is said to achieve
superior drying efficiency compared to both compressed air and other
blower-driven solutions. The drying design delivers air at high velocity
very close to the surface of the product, breaking the surface tension of
the retained water and allowing it to be removed.
Utilising high efficiency blowers, ACI’s DRI-Line Powerpack delivers
warm (80
o
C/176
o
F) clean, contaminant-free air at constant volume
and pressures to ensure the drying process is consistent and reliable.
It also has the advantage of being ‘plug and play’ as it runs off a
230V, single phase supply. A version with a 110V supply will also be
available shortly.
The unit can dry extruded products from 5mm to 25mm diameter at
speeds in excess of 300 m/min. Its drying effectiveness is achieved by
passing extruded product through a pair of hinged drying heads that
deliver the high velocity airflow directly to the product. The hinged
heads are sprung allowing any defect/knot to pass through without any
requirement for adjustment.
The blowers used in the Powerpack are housed in a sturdy, stainless steel acoustic chamber that keeps noise levels well
below 85dB(A). The drying heads are predominantly fabricated from stainless steel, but also utilise polyethylene for the main
facing plates and plenum chamber end-caps for its hardwearing properties.
Extensive customer field trials of the DRI-Line Powerpack suggest significant energy savings are possible, compared to
compressed air systems, and short payback times. ACI is offering free on-site trials to potential UK users.
Air Control Industries Ltd – UK Website
:
www.aircontrolindustries.comDRI-Line Powerpack wire and cable dryer from
m
m
Air Control Industries
(1) Casting machine, (2) sensor arm, (3) manual bar shear, (4) conveyor, (5) Micromill 69/7 – based on the use of 7 three-roll stands
m
m
model 69 (6) rod deflector and basket coiler, (7) Additional breakdown mill to upgrade production in a second step.
Aluminium and copper rod lines for any demand