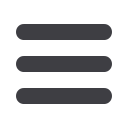

June 2015
AFRICAN FUSION
17
Figure 1: SEM images of the pre-alloyed IN100 powder: (a): low magnification
showing the powder size and morphology; (b). higher magnification showing
carbide precipitates at grain boundaries.
Figure 2: Microstructures of as-deposited IN100: (a): multiple layer
development on the cross-section normal to the scanning direction; (b):
magnified view of the microstructure showing columnar grain structure.
tion results of the laser-processed samples showed desirable
microstructures.
Experimental procedure
The experiments were carried out using a laser aided additive
manufacturing system which was developed at Singapore
Institute of Manufacturing Technology. The cladding head
with coaxial powder feeding was mounted on a CNC sys-
tem which was enclosed in a metallic chamber to prevent
operators from accidental injury by laser radiation. A 500 W
fibre laser system (IPG Photonics), operated in CW mode at
a wavelength of 1 070 nm, was used in this study. Argon gas
was used as the powder carrier gas as well as the shielding
gas to prevent the melt from undergoing rapid oxidation at
elevated temperatures.
Powder was delivered to the cladding head by a powder
feeder (Twin 10-C, Sulzer Metco). Process parameters included
CW laser power of 150-250 W, scanning speed of 5-10 mm/s,
andoverlapping of 50%. Commercially available, gas atomised
IN100 powder (IN100) was used in this study. The gas atomised
powders had an average size of 20-45
µ
m in diameter andwere
used as received. Table 1 shows the chemical composition
of the IN100 powders and substrates and Figure 1 shows the
morphology and microstructure of the IN100 powders.
For the deposited IN100 samples, it was necessary to per-
form heat treatment in order to relieve the residual stresses
as well as enable the precipitation of strengthening phases.
Heat treatment consisted of a solution treatment at 1 080 °C,
followed by a two-step age hardening sequence wherein the
parts were held at 845 °C and then 760 °C to fully develop the
strengthening phases.
As part of the sample preparation procedure, both the
as-deposited and heat-treated samples were sectioned and
polished down to 0.05
µ
m finish. Samples were then etched in
two ways: First was chemical etching (1 part 30%H
2
O
2
, 2 parts
HCl, 2 parts distilled water) for grain structure observation;
and second, electrolytic etching (LectroPol-5, Struers) by
Struers’ A-2 etchant (78 ml perchloric acid, 120 ml distilled
water, 700 ml ethanol, and 100 ml butylcellosolve) at room
temperature using 9-10 V and etching times of between two
and 4 four seconds. Electrolytic etching reveals the
γ
′ phase
while the
γ
matrix is dissolved.
Microstructures were examined by optical microscopy
(OM) (MX51, Olympus) and scanning electron microscopy
(SEM) (EVO-50 & ULTRA plus, Carl Zeiss) with simultaneous
elemental analysis using energy dispersive X-ray spectros-
copy (EDS) (X-Max, Oxford Instruments) and texture analysis
by electron backscatter diffraction (EBSD) (HKL Channel 5,
Oxford Instruments).
Crystalline phases were analysed using X-ray diffraction
(XRD) (D8 Discover, Bruker) with a radiation source of Cu K
α
(
λ
=1.54060 Å). The volume fraction of
γ
′ to
γ
and the average
grain size of the
γ
′ phasewas determined using image analysis
software (analySIS pro, OLYMPUS).
Results and discussion
Microstructures of as-deposited and post heat-
treated components
As shown in Figure 2, microstructures of as-deposited samples
revealed the pattern of layer-by-layer deposition and the over-
lapping of the scan tracks produced by laser processing. The
layer thickness was found to be approximately 300
µ
m and
Figure 3: Microstructures of post heat-treated IN100: (a): multiple layer
development on the cross-section normal to the scanning direction; (b):
magnified view of the microstructure showing various sizes of equiaxed and
columnar grains.
the heat-affected zone (HAZ) was seen as a white trace using
optical microscopy as shown in Figure 2a.
Two types of dendritic structures were observed (Fig-
ure 2b): a columnar dendritic region and fine equiaxed
dendrites. The columnar dendrites grew epitaxially from the
partially remelted grains of the previously deposited layers,
which acted as the nuclei for directional growth of the crystal
[1]. Dendrites typically grew along the build direction [001]
because the cooling of the melt pool was primarily via the
substrate or previously deposited layers and partially via the
adjacent solidified deposited layer. A similar observation has
been reported as the directional growth of the dendrite was
opposite to the heat flux direction, which was perpendicular
to the substrate of the laser deposited samples [14, 15].
The effect of post-deposition heat treatment on micro-
structure is shown in Figure 3. The formation of a new grain
structure by the diffusion process during heat treatment was
observed as the microstructure had lost its dendritic charac-
teristic. The grain size distribution was not uniform because
each layer was composed of three different regions. As seen in
Figure 3b, relatively finer grains of average diameter less than
30
µ
m were concentrated at the lower part of each layer, i.e.
at the bottom of the melt pool. These small equiaxed grains