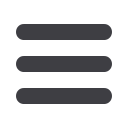

30
MODERN MINING
December 2015
MATERIALS HANDLING
feature
electrical failure or overheating of the conveyor
belt motors.
He offers the following outline of common
causes of fire on conveyor belt systems:
Friction due to a belt losing traction and slip-
ping on the drive roller, or due to a misaligned
belt slipping off the jam rollers and jamming.
This can generate sufficient heat to ignite the
belt itself or the product it is transporting.
Cutting or welding activities generate hot
moltenmetal particles that can ignite the belt.
Accumulatedwaste below the belt due to lack
of regular housekeeping.
Overheated materials from ovens, kilns or
dryers that have not been sufficiently cooled
before being placed on the conveyor belt.
Undetected electrical malfunctioning of con-
veyor belt motors.
To ensure early fire detection in conveyor
belt environments, ASP Fire recommends the
installation of a variety of Technoswitch fire
detection technologies, which are especially
suited to long-distance and moving environ-
ments. These include:
The 246-1 Ember Detector, which recognises
a smoldering ember on a moving conveyor
belt before it bursts into flames.
A linear heat detection cable, which is used
for very long distances – common with con-
veyor belt systems – and responds to a rise
in heat that is above the alarm threshold.
The 40-40 IR3, which uses three different
infrared light wavelengths to detect an open
flame.
The TEC247, a fire control panel that manages
all of the detection devices, the alarms and
the suppression equipment valves.
The TEC057-1, an interface unit that allows
for multiple suppression systems or cylinders
to be connected to a single fire control panel.
Over and above this, van Niekerk recom-
mends other industry-leading technologies for
cost-effective conveyor belt fire-suppression:
“The I-Cat Firetrace self-activating fire-
detection and suppression system is a prime
example. This technology can automatically
detect fire and effectively suppress it in a mat-
ter of seconds before it becomes a problem.”
The Firetrace system boasts polymer tub-
ing that will rupture when exposed to a flame.
The specialised Firetrace detection tubing
reportedly combines leak resistance, flexibility,
durability and precise temperature sensitiv-
ity, allowing it to react quickly when the heat
from a fire is present. It connects to a custom-
engineered valve and a Firetrace cylinder that
contains the best fire suppression agent for a
particular hazard.
“These low-pressure systems cause no ther-
mal shock, have long operational life, allow for
on-site refilling of the systems, are electrically
non-conductive and use sustainable, clean
technology, and can even be used with other
external fire detection systems,” explains van
Niekerk.
The I-Cat T-Rotor Technology systems are
another example of innovative technology
– providing localised protection, hand-held
extinguishers, fast response back-packs and
vehicle protection systems. They comprise
extinguishers that use a combination of water
The Backpack water mist
system being used on a fuel
spill fire. The environmen-
tally friendly system rapidly
extinguishes 250 litres of
burning fuel using 12 litres
of water. According to ASP
Fire, this has the same knock
out power as a 500 litre
trailer-mounted system.