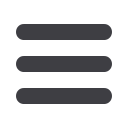

December 2015
MODERN MINING
33
MATERIALS HANDLING
C
onveyor belt slip-
page, poor trac-
tion, inferior wear
properties and inad-
equate water shedding
are nightmares which
plague plant operators
on mines. All of these
can cause unplanned
downtime with associ-
ated cost implications.
However, more criti-
cally, conveyor belt slip-
page is potentially dan-
gerous and could even
result in catastrophic
failure in a plant. In in-
stances where slippage
continues, there is an increased danger of fire as well as damage to
the carcass and splice, caused when the belt does not grip.
This is according to Mark Jarrett, National Sales Manager of
Multotec Wear Linings, who says that the company’s MultoLag™ pul-
ley lagging functions as a maintenance-free, wear-resistant cover that
is applied to pulley shells to improve traction in the case of drive pul-
leys and provide a polished low friction surface on non-drive pulleys.
MultoLag™ has become a widely accepted solution for mining and
industrial operations as a cost effective response to these recurring
problems. “This lagging is particularly effective in aggressive condi-
tions, even on bucket elevators or where material is inevitably trapped
between the pulley shell and the conveyor belt. It is suitable for wet
conditions and other applications where a low coefficient of friction
or a high level of traction is required on drive pulleys or where general
wear protection of the non-drive pulley is needed,” Jarrett says.
He points out that traditional rubber or epoxy pulley lagging has a
much shorter lifespan than ceramic lagging.
The MultoLag™ system uses standard smooth high alumina ceramic
tiles for non-drive pulleys and studded tile lagging for drive pulleys.
The smooth/polished surface provided by the very hard ceramics on
the non-drive pulleys provides minimal friction, less resistance and
therefore no wear. Conversely, the studded tiles on the drive pulleys
have a high coefficient of friction of 0,78, which means no relative
movement between the surface of the ceramic lined drive pulley and
the surface of the conveyor belt. What is significant is that without
relative movement between surfaces there can be no wear.
Ceramic lined drive pulleys are covered with high density
20 mm x 20 mm x 6 mm ceramic tiles, with 1 mm high round-edged
studs on the tile face that create maximum traction, without the asso-
ciated damage to belts. The 6 mm thick high density smooth ceramic
tiles are bonded directly to the pulley’s surface with specially formu-
lated Multotec Hi-Bond epoxy.
“This epoxy allows us to achieve a bond strength at least 70 % higher
than that of rubber to steel or rubber to ceramic. It also allows for sur-
face flexing, corrosion protection and water dissipation. In the unlikely
event that patching is required, local damage can be repaired quickly
without removing the surrounding pulley lining,” Jarrett says.
MultoLag™ pulley lagging functions as a mainte-
nance-free, wear-resistant cover that is applied to
pulley shells to improve traction in the case of drive
pulleys and provide a polished low friction surface on
non-drive pulleys.
Lagging
system reduces costs