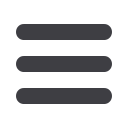

December 2015
MODERN MINING
31
MATERIALS HANDLING
feature
and/or foam in a mist form, as opposed to tra-
ditional fire extinguishers that use either dry
foam or chemical powders.
“The misting technology of the T-Rotor
Technology uses a small rotor unit that atom-
ises water and charges it with kinetic energy,
creating a fine atomised mist at a water pres-
sure of 3 bar in a mobile unit. Using water as
the main agent, and nitrogen as a propellant, it
can extinguish all types of fire, including rub-
ber and plastic fires, kitchen cooking oil fires,
diesel and petrol fires and electrical fires rated
up to 245 kV,” explains van Niekerk.
The system can also be designed to create
cooling zones on conveyor belts to detect and
cool hot material – without adding to the mois-
ture content of the product – to reduce any
potential fire risks.
Van Niekerk ends by noting that the Water
Mist extinguisher range is SABS-approved:
“Using water and nitrogen is safe, effective and
saves on maintenance and service costs. Each
litre of water amounts to 120 m
2
of coverage
capability, and the small quantity of water that
is used has the added benefit of ensuring little
to no redundancy, damage or environmental
contamination.”
CMA holds ‘Industry Indaba’
At the International Materials Handling Conference – Beltcon 18, held in Jo-
hannesburg on August 5 and 6, 2015, members of the industry mandated
the Conveyor Manufacturers Association of SA (CMA) to investigate two is-
sues. These were preventing runback in conveyors and the nip guard gap.
The CMA hosted an important and successful ‘Industry Indaba’ in Octo-
ber 2015 to discuss not only these two items, but two more in addition – a
report-back to inform industry that the recently repaired mid-scale gallery
test apparatus at the SABS is once again available for testing of fire retardant
belting; and pull key stations.
The format of the Indaba consisted of four presentations on the above
matters of concern, followed by debate from the floor. The four topics on
the agenda were:
Part 1 – Legal requirements for preventing runback in conveyors. Simon
Curry (Flexco, CMA Chairman).
Part 2 – Legal requirements pertaining to nip guards. Alan Exton (Accrete
Consulting).
Part 3 – Legal requirements for testing of fire retardant belting (SANS
971). Paul Nel (ThyssenKrupp).
Part 4 – Legal requirements pertaining to pull key stations. Alan Exton
(Accrete Consulting).
Each topic informed delegates of the legal requirements relating to the
specific area of concern, which was followed by debate from the floor.
The CMA was mandated to establish a working group to further investi-
gate the nip guard gap and pull key stations. These are currently in the pro-
cess of being formed, and it is envisaged that the working group will consist
of all stakeholders, but mostly driven by the users and managed by CMA.