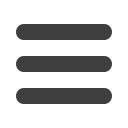

48 l New-Tech Magazine Europe
motion tracker with advanced
motion sensing technology
is ubiquitous in applications from
image stabilization in miniature
cameras to control and navigation
applications for UAVs. A MEMS-based
IMU is the preferred motion sensing
technology in industrial applications.
The MEMS-based IMU’s increasing
adoption rate and ever growing list
of possible applications is a direct
result of the technology’s versatility –
high achievable target performance,
highly reliable solid state technology
in a very small form factor with very
competitive pricing. The technology
is also very attractive for high-volume
consumer applications.
The various facets of the MEMS-based
IMU motion sensing technology
offer a plethora of possibilities –
it can be both a boon and a bane!
While a wide range of sensing
components with varying grades of
performance, size, integration levels
and costs is very attractive, it can be
very counter-productive for a team
and the execution of the project.
Opting for a MEMS-based IMU
with the desired specifications and
developing peripherals from scratch
can take time and resources away
from the actual development of the
target product. This blog explains
the thought processes that go into
delivering a state-of-the-art motion
tracking module with different
integration possibilities designed to
suit your application needs.
Sensor characterization and sourcing
Integration of inertial sensing starts
with finding the right technology for
the application. MEMS-based IMU
motion sensors are available in chips
at far less than $1 per axis, but the
price range can exceed more than
$100,000 per axis for optical inertial
sensors. Next to the cost, there is
also the aspect of suitability for an
application. Even when considering
MEMS-only inertial sensors, there
is a huge variety of sensors. Some
sensors have better performance
under vibration, some have a good
long-term stability and others may
have low noise. The key is to find the
sensor that best fulfills the need.
Simply understanding the sensor level
specifications needed for a certain
application can pose the biggest
challenge. Often an application
oriented development team can state
(and get) requirements in terms or
orientation accuracy needed or other
high level functional specifications.
Breaking these down to sensor level
specifications is often much more
difficult because of lack of time to dive
into the specifics of the underlying
technology.
There are several ways to find the
best sensor, from comparing data
sheets to doing a full characterization.
As data sheets are not uniform and
data is not always available for all
conditions (e.g. vibrations, lateral
acceleration), a full characterization
targeted to your functional level
A
A Motion Tracking Module for Your
Application
Marcel van Hak and Arun Vydhyanathan, Fairchild Semiconductor