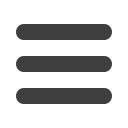

50 l New-Tech Magazine Europe
30 mg (~2 deg roll/pitch error) are
not an exception in low-cost MEMS
sensors. Gyroscopes biases of up to
30 deg/s are also possible, although
most gyroscopes biases are between
-5 and 5 deg/s. A calibration improves
the gyroscope bias repeatability up to
+/- 0.5 deg/s, whereas accelerometer
biases are limited to 2 mg (0.1
deg roll/pitch error). Mounting a
module on another board does not
influence the calibration parameters.
As modules are simultaneously
tested during calibration, production
yield of the end-user application is
significantly improved.
The capital investments for a
calibration and test setup are
significant, especially when the
number of sensors per year is limited
(under 10,000 units per year). In
cases in which fewer than 10,000
units per year are required, the test
and calibration costs already justify
the higher price of a module.
Electronics and Mechanical Design
With magnetometers in many IMU
designs, and with sensitive MEMS,
the electronics design cannot be
overlooked. Mechanical stress is
motion or high magnetic dependency.
Performance testing on a wide range
of test platforms ensures the best
performance for many different
applications. An added benefit
of using Fairchild’s sensor fusion
software is that the sensor fusion
algorithm outputs different data in
selectable output formats. Examples
are free acceleration, where gravity
is already subtracted; reference
coordinate frames, for use in arbitrary
alignment; and several fixed point
and floating point output formats.
Getting all this in a tested package
will save you a lot of time and risk in
the execution of your project.
The motion tracking module was
designed keeping in mind user
requirements and application needs.
The design and development process
took into thorough consideration
the various aspects of producing
and delivering a robust and high
performance motion tracker module.
often specified for the relatively large
MEMS sensors components, so this
should be taken into account. When
something changes in the MEMS
sensor component itself, the PCB of
the end-user application may need
to be redesigned. A turnkey module
solves all these issues as it comes on
a PCB that does not change interface
and pinning and relieves the user
from mechanical stress calculations.
Sensor Fusion Software
Sensor fusion software is required
to interpret MEMS sensor data as
useful orientation data, should the
application demand this. Although
sensor fusion algorithms are
documented in literature, it is not as
straightforward as just taking data
and applying a filter. The sensor fusion
algorithms of Fairchild’s FMT1000
series modules are optimized for
several different use case scenarios
based on the decades of application
experience of Xsens, an industry
leader in motion tracking acquired by
Fairchild. The sensor fusion algorithm
can be processed with different sets
of settings, such as dynamic, human