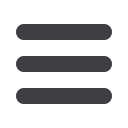

M
ARCH
2016
159
4-8 April 2016
Composite tubes with powerful bonding
HOESCH Schwerter Profile GmbH
develops its products in collaboration with
specific fields of industry and customers.
Modern power stations and industrial
plants are just two areas where special
steel solutions are used that are required
to withstand the most extreme loads.
The classic seamless steel tube for
pressure vessels is a key construction
element in the building of thermal plants.
The requirements for boiler construction
steels become significantly more
exacting if – instead of conventional
boiler fuels such as coal, oil or gas –
other sources of energy are used that
result in strongly corrosive combustion
products. For instance, boiler tubes in
a waste incineration plant are not only
exposed to thermal loads, but are also
subject to corrosive attack, triggered by
the chemical element chlorine.
For this specific application, the
conventional boiler tube used in plant
construction with its proven component
strength was equipped with a ‘coating’
using a corrosion-resistant austenitic
material. The intention behind this
combination of materials is to allow
the carbon steel to handle the thermal-
mechanical load on the tube, while
the austenite provides protection
against corrosion from the prevailing
environment.
‘Combined materials’ tubing of this
kind is often referred to as composite.
If produced using the extrusion process,
the term used to describe this is co-
extruded tubing. The high temperature
structure steel and high alloy layer are
formed simultaneously during the hot
extrusion process at temperatures from
1,150°C to 1,250°C.
The development of composite
tubing pursued by Hoesch Schwerter
Profile was undertaken with the aim of
overcoming the known disadvantages of
clad pipes.
The carbon steel component and
austenitic layer of the extrusion billet are
manufactured in a common hot forming
process at around 1,150°C to 1,250°C.
The metallurgical connection between
the two materials is achieved in the
solid state using pressure-accelerated
solid state diffusion. A diffusion zone
approximately 10μm thick forms between
the materials, which is responsible for a
high-strength, oxide-free metallurgical
bond of materials.
The fine microstructure configuration
of the layer and base material is
preserved, with no variation in the alloy
concentration.
Hoesch Schwerter Profile GmbH
–
Germany
Email:
info@hoesch-profile.comWebsite:
www.hoesch-profile.comExtruded tubing with internal
and external layer
S
t
a
n
d
n
o
.
3B22
THE ORIGINAL