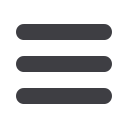

32
MODERN MINING
March 2015
MATERIALS
HANDLING
T
he company behind the system
is Johannesburg-based Deebar,
which was established in the mid-
1970s by Dereck Soekoe, who is
the current CEO, and whose two
sons, Desmond and Brandon, now assist him
in the running of the business. Deebar origi-
nally made its name as a supplier of mine
shaft signalling systems and this is still its
core business although its market offering has
now grown to encompass many other products
such as station stopping devices, mine com-
munication devices and switchgear, starters
and Fortress interlocks.
The Deebar Rail-Veyor
®
is a relatively recent
diversification, with Deebar’s involvement in
this technology dating back to 2004. The first
mine to adopt the system was Harmony Gold’s
Phakisa operation near Welkom, which placed
an order with Deebar in 2005. The Phakisa
installation – which is underground and just
over 5 km in length – has now been running
since 2007 and has proved very successful.
In fact, when
Modern Mining
visited Phakisa
several years ago, a senior Harmony Gold
executive, Tom Smith (then responsible for the
group’s South African operations although he
has since moved on), told the magazine that
Harmony was delighted with the system.
“In terms of capex, it cost roughly R18 mil-
lion to install whereas a conventional rail
system, the main alternative we looked at,
would have set us back R30 million,” Smith
said at the time. “Operating costs are also excel-
lent – approximately 30 % less, we estimate,
than a rail system on a cost per ton basis.” He
added that installation time was also much less
with the Deebar Rail-Veyor
®
– six months as
opposed to about 24 months.
Comments Desmond Soekoe: “Phakisa
was the first commercial Deebar Rail-Veyor
®
application in the world and represented
something of a learning curve for Deebar, as the
system was basically conceptual at the time we
received the order. A great deal of credit must
go to Harmony Gold, which essentially backed
an unproven technology. Thankfully the system
is now working extremely well – although it
was not without its teething problems, which
all had to be addressed and rectified.”
Deebar has now placed its Rail-Veyor
®
busi-
ness in a newly established company within
the Deebar group, known as Deebar Rail-Veyor
®
.
The Deebar Rail-Veyor
®
contract in North
West Province has been carried out on a turn-
key basis by Deebar and encompasses the
design, manufacture, installation and commis-
sioning of the system. In essence, the Deebar
Rail-Veyor
®
will collect ore from two separate
stockpiles and transport it to the stockpile
feeding the concentrator. Currently only two
trains have been installed but once in full pro-
duction three will be needed, with each train
consisting of 140 cars, each 2,14 m long. By
comparison, the Phakisa Rail-Veyor
®
has 296
cars per train.
The project includes all track work, an
incline structure to accommodate a tipping
loop approximately 20 m high to allow the rail
cars to tip onto the plant stockpile, and a return
loop to get the trains back on track for the load-
ing section.
The Deebar Rail-Veyor
®
was chosen for
Another Rail-Veyor® system
in
The latest Deebar Rail-Veyor® system to be installed at a
South African mine is now operational at a site in North
West Province. The systemwill ultimately consist of three
trains and will move up to 525 000 tonnes of ore a month
over a distance of 2,2 km. It is expected to deliver a 30 %
reduction in energy consumption compared to a conven-
tional surface conveyor belt.