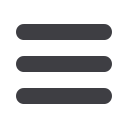

34
MODERN MINING
March 2015
many enhancements over the Phakisa Rail-
Veyor
®
. These include a new tubular design
for the supporting structures, a pneumatic
tensioning system, a braking system and a
new SCADA logging reporting system, which
will deliver accurate production statistics to
management.
Most readers of
Modern Mining
will be
familiar with the Deebar Rail-Veyor
®
concept
but, to recap, it is a bulk material transport
system described by Deebar as being based on
the principle of a roller coaster, where a train
consisting of a series of articulated trough-
like, two-wheeled cars runs on light rails up
inclines, down hills and around bends on a rail
that can turn back 180 deg within 30 m. Each
car is connected to the car in front by means
of a swivel clevis that allows articulated move-
ment for curves and dumping. Sealing of the
gap between cars is maintained by the use of
overlapping flexible rubber flaps that prevent
spillage of the material and also operate as dis-
charge chutes for dumping the load.
Traction is provided by a number of equally
spaced, energy efficient, dual drive stations,
together with tyres in contact with the side
drive plates of the cars, thus providing forward
thrust. Drive stations only switch on through
sensors as the train arrives near a drive sta-
tion and switch off once the train has passed
through. This means that at any one time only
two sets of drives are running per train, result-
ing in a major saving in energy costs.
An interesting question is whether the
Deebar Rail-Veyor
®
can be described as a South
African development, given that a company
based in Canada also offers a similar system
under the same name. According to Desmond
Soekoe, it most certainly can. “The concept
on which Rail-Veyor
®
is based was developed
in the 1960s by SECCAM, the French railroad
operator, but the technology to make it work
– such as variable speed drives and fibre-optic
communications – didn’t really exist at that
time,” he explains.
“The point to stress, however, is that the
installation at Phakisa was entirely a South
African designed and engineered system and
was the very first commercial application in
the world. We own the intellectual property
rights to the system as installed at Phakisa and
have taken out a number of international pat-
ents on aspects of the technology – for example,
the hydraulic drive stations. We manufacture
all the elements of the system locally, for the
most part in our own workshops. Our only real
technology partner is Mitsubishi, represented
locally by Adroit Technologies, from whom
we source the variable speed drives and the
PLCs we use.”
An advantage of the Deebar Rail-Veyor
®
is its
ability to adapt to a customer’s existing infra-
structure. As Soekoe says, “The system can
handle bends of up to 30 deg and inclines or
declines of 11 deg, which would all pose prob-
lems for its competitors – locos or conventional
conveyors. The Phakisa installation, for exam-
ple, has six 30 deg bends along the route and
climbs a 1 in 200 incline on the return side of
the dedicated haulage route. Design is very site
specific and each installation is customised to
meet the needs of the site and, of course, the
The North West installation
features a new tubular
design for the supporting
structures, a pneumatic
tensioning system, a
braking system and a new
SCADA logging reporting
system.
MATERIALS
HANDLING