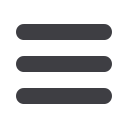

24
MODERN MINING
September 2016
COAL
The decline conveyor seen from the box front. It has a belt width of 4,6 m/s and is rated at
2 900 tph. The extension of the conveyor under the box front was undertaken over four days
in May this year.
Above:
Simplified cross
section through the bunker
and box front.
had at every step of the way from our client,
Sasol Mining.”
The bunker feeds ore to the decline con-
veyor which has a capacity of 2 900 tph and
a belt speed of 4,6 m/s. With this capacity,
the conveyor system can empty the bunker –
assuming no inflows – within 27 minutes.
Describing the bunker, Wells says it has a
finished diameter of 14,7 m and extends 24 m
down from the 4 Seam horizon (200 m below
surface) to the soffit floor of the box front
chamber. The bunker has a cylindrical section
of 16,5 m and – below that – a conical section
of 5,5 m. The box front chamber extends a fur-
ther 10 m to the footwall of the decline on the
2 Seam horizon.
According to Wells, the first task was to
create a collar ring beam at 4 Seam level to
facilitate excavation of the bunker. “To do an
excavation of this type, you need a decent infra-
structure,” he says. “So we excavated a top cut
to a depth of 1,8 m using an LHD and an exca-
vator. The ring beam itself has dimensions of
1 m x 1 m and – including approach slabs –
required 200 m
3
of concrete to be poured. To
excavate the barrel of the bunker, we opted to
use drop raising to sink a 4 m diameter cen-
tre core which was then slyped out to the full
diameter of 14,7 m. We supported the side-
walls as we advanced using mesh, shotcrete
and rock anchors. In all, the bunker excavation
amounted to 5 800 cubes.
“To establish the profile of the conical sec-
tion – which we only did earlier this year once
the box front was completed – we used sand-
bags to form a back shutter and then backfilled
behind these bags with mass concrete. In all,
we used 6 800 sandbags during this phase of
construction.”
He adds that the volume of shotcreting was
huge with 450 cubes of mass fill shotcrete being
required for backfilling with an additional
126 cubes of 70 MPa andesite shotcrete, 300 mm
thick, being placed on two layers of mesh as
the final step in the operation. “This andes-
ite shotcrete was very unforgiving in terms of
pumpability and flowability,” notes Wells.
While the excavation of the bunker was
by no means an easy task, the construction of
the box front – which houses the chutes and
vibrating feeders controlling the discharge of
coal to the decline conveyor system – proved
equally demanding. “Put simply, this is primar-
ily a steel structure but with massive amounts
of concreting required for the floor slab, the
16,5 m long, 10 m high and 1 m thick east and
west side walls and the 1,5 m thick soffit or
roof,” he notes. “Altogether we poured over
1 800 m
3
of concrete. Given the dimensions of
the side walls, we elected to make use of wide
scaffolding. These walls, incidentally, each
required 30 tons of reinforcing.”
The main elements of the steel structure (the