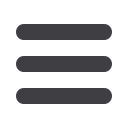

News
Technology
July 2016
39
www.read-eurowire.comAs manufacturers look to lightweight
materials for improved fuel economy,
the associated fastening problems
necessitate zero defects through 100
per cent inspection.
Manufacturers looking to reduce weight
(or for cost savings) have turned to
lightweight materials like aluminium,
plastics, zinc and magnesium.
The associated fastening issues require
zero defects as production speed and
quality depends on them.
The fastener industry is increasingly
relying on higher resolution 3D
inspection of billions of fasteners.
Gauging, sorting and cylindrical part
inspection systems incorporating laser,
vision and eddy current for dimensional
measurement
and
determining
metallurgical defects are now used
for high-speed inspection of many
fasteners.
The
introduction
of
lightweight
materials has made zero defects a
particular challenge when the fasteners
are still steel.
Quality control is critical because even
small defects can cause big problems
in working with lightweight materials,
such as having to rework engine blocks
if male threaded fasteners strip out of
threaded holes.
To address these production and quality
issues, the increasing use of lightweight
materials is requiring high-speed 100
per cent fastener sorting as well as more
inspection capability from fastener
sorting machines.
Laser and vision-based machines can
provide 100 per cent high-speed 3D
fastener inspection.
General Inspection, for example, uses
3D information from multiple laser
beams to detect defects that may only
be on one side of the part, such as
damaged threads.
Laser topography can provide a
detailed 3D image of the part, detecting
dents, flatness, chips and dimensional
characteristics.
General Inspection – USA
Website
:
www.generalinspection.comEliminating defective fasteners
▲
▲
Laser topography can provide a detailed 3D image of the part, detecting dents, flatness, chips and dimensional
characteristics