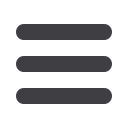

July 2016
40
www.read-eurowire.comNews
Technology
For more than 40 years Sikora, one of
Germany’s successful mid-size companies,
has stood for quality, service and cost
saving in the areas of measuring, control,
inspection, analysis and sorting systems.
During this time, special attention has
been paid to innovation. This does not
only apply for the future-orientated
research and development work – also
the external appearance is always one
step ahead.
An example of this innovative orientation
is the new advertising campaign that
uniquely presents Sikora devices in use.
“Nowadays,
pure
product
pictures
are not sufficient any longer to stand
out from the technically oriented
environment,” said Katja Giersch, head of
corporate communication. This has been
the challenge of the new advertising
campaign, which has been placed
in hose and tube as well as plastics
trade magazines worldwide since the
beginning of 2016.
“Therefore, we consciously combined the
technology with people, in order to offer
the viewer a functional and emotional
access. Presented are Sikora products
in
a
manufacturing
environment.
Furthermore, each image shows a
Sikora employee, who is responsible for
the development, assembly or service
of the corresponding device. We are
demonstrating
therefore,
that
our
products are backed by a strong team,”
added Mrs Giersch.
The unique image style, which was specially
created for this campaign, underlines the
innovative orientation of the technology
company. Furthermore, the colour scheme
changed: instead of a minimalist black
design, Sikora puts the focus on clear blue
and white shades, which support the
expressive large image stages.
The advertisements are completed by
a communication area, on which all
benefits of the displayed technology are
clearly highlighted for the user.
Sikora AG – Germany
Website
:
www.sikora.netTechnology in a beautiful form at Sikora
▲
▲
The Laser6000 series from Sikora
Plasmait has introduced a new PV
ribbon line design with an improved
output, featuring a maximum speed of
210m/min. This allows the production
of up to 250 tonnes of PV ribbon per
annum in a typical production split
between interconnect and bus bar
ribbons.
Interconnect ribbons are typically 0.8 to
2mm wide and 0.1 to 0.2mm thick. They
are usually coated with about 20 micron
thick layer of solder. Bus bar ribbons are
larger and typically range from 5 to 6mm
width.
The new line can produce ribbons
with yield strength down to 50MPa
(Rp0.2%). These super-soft ribbons are
spooled onto the integrated version of
a single-head, precision take-up with
accumulator. This allows copper ribbons
on payoff spools to be continuously
annealed, tinned and spooled onto
4kg-5kg
spools,
without
process
interruption. Some producers choose to
equip the line with an automatic spool
changeover unit that can be integrated
with the take-up unit.
Some producers also opt for an
integrated line with an inline rolling mill
to produce interconnect ribbons directly
from round copper wire.
The line’s total output can benefit from a
double-stand rolling mill that operates at
line speed. The plasma tinning line operates
without chemical cleaning and fluxing
whilst rolling runs without cooling agents,
which makes the whole production dry and
environmentally friendly.
Round wires can also be produced on
the line, with mounting of appropriate
wiping
system
for
round
wires.
Traditional tinning lines require acid
cleaning, rinsing and fluxing prior
to tinning. Plasmait’s line operates
without flux, which avoids expensive
contamination of a tin bath and thereby
reduces the cost of tin waste.
High output, approximately 95 per cent
up-time and a high level of automation
allow PV ribbon producers to reduce
labour costs and reduce scrap rates whilst
improving production consistency and
product quality.
Key benefits include:
•
High-speed production with up-times
over 95 per cent
•
Production of super-soft PV ribbon
•
High quality finished product and low
scrap rates
•
No solder waste due to flux
contamination (flux-free production)
•
Automated and computer-controlled
production
•
Limited manual involvement, ie low
labour cost per ton of production
•
Low maintenance cost and low
energy consumption
Additional original manufacturer services:
•
Commissioning, startup and full
operator training
•
Advanced operator and production
manager training
Plasmait GmbH – Austria
Website
:
www.plasmait.comNew high-speed PV ribbon line
▲
▲
The new PV ribbon line from Plasmait