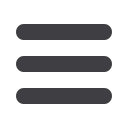

January 2017 TUBE PRODUCTS INTERNATIONAL
17
business & market news
and expanded within the pipe to both
grip the inner diameter and also form a
seal. The Test End normally has a valve
attachment that enables water or air to
be passed into the pipe and pressurised
up to 16 bar. This made them suitable
for the purpose required for the HDD
installation. The problem was how to get
them into the Multi Puller and have them
work effectively as pulling heads while
still enabling them to be used to pass
ballast water into the pipes.
The modifications to the Multi Puller and
the Test Ends involved, within the nose
section of the Multi Puller, connecting
all the Test Ends to the towing plate
such that they were rigidly held in place.
The individual pipes were placed over
the grippers of the Test Ends, which
were then expanded to hold the pipes
in place. As added security, to ensure
that in gripping the pipes they did not
expand or deform at the towing end,
each pipe was fitted with a stainless
steel collar to offer a platform against
which the Test End could seal and grip.
The Test Ends were then connected
together so that the contractor, when
putting water into just one of the 125mm
diameter pipes, could fill all the pipes
to the same level at the same time.
Using this design not only enabled the
contractor to fill the pipes with ballast as
and when required, but also meant that
the full length of the pipe string did not
have to be welded together and laid out
before the final pull-in operation could
take place.
Once thepull-inoperationwas underway,
new lengths of the pipe string could be
welded into place as required, with the
final lengths being added just prior to
the time when the ballast pumping was
needed. Having connected together the
pipes at the towing head, using just one
of the smaller diameter pipes meant that
all the pipes could be ballasted at the
same time.
With this plan in place, once the
main boring and reaming work was
completed, the pipe bundle was
assembled and leak tested and the pull-
in operation commenced.
The operation was successfully com-
pleted without incident.
Pipe Equipment Specialists Ltd
– UK
enquiries@pipe-equipment.co.uk www.pipe-equipment.co.ukStockton Drilling Ltd
– UK
info@stocktondrilling.com www.stocktondrilling.comAlloy 200/201
Alloy 400
Alloy 600
Alloy 625
Alloy 825
Alloy C276*
*
seamless & welded
www.hartbv.nl|
sales@hartbv.nlLEADING STOCKHOLDER
IN NICKEL ALLOYS
Seamless Pipe and Fittings
hart bv ad 1-6.indd 1
03-11-16 13:52
Detail of the final reamer/towing head/pipe bundle assembly
Multi Puller and Test Ends