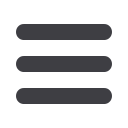

W
elding
T
echnology
www.read-tpt.comM
ay
2010
99
›
POLYSOUDE’S launch of the P6 300
ampere mobile TIG welding system for tube
assembly, using automated orbital welding,
opens up new production possibilities
for plant construction – technologically,
economically and qualitatively. This is made
possible by intuitive operation combined
with a modular system concept.
A large touch-screen provides the
human-machine interface. All interactions
with the system take place via this interface,
which issues all commands to the internal
electronics via the software and transmits
the status of the joining process to the
operator.
The P6 has autonomous system
configuration and auto-programming,
and also features real-time welding data
recording for reproducible welding results.
The machine not only detects the type of
tool connected (such as open or enclosed
weld heads), but also knowswithinwhich limit
values the tool can work. Auto-programming
adjusts the welding parameters down to the
last detail.
Other features include program control
by time or angular degrees calibrated in mm/
min or inch/min; error-diagnostic system;
a built-in printer for welding procedure
archiving and documentation; Ethernet
compatibility; closed loop regulation of torch
rotation and wire speed; arc voltage control
Orbital welding power source with
6 axes and auto-programming
P6 power source with CNC control for orbital
and mechanised welding
The system features an intuitive touch-screen interface
(AVC) and torch oscillation control (OSC);
torch gas control with safety valve and flow
detection; and closed loop water cooling
system with safety valve for welding head
and torch.
Polysoude SAS
– France
Fax: +33 2 4068 1188
Email:
a.husson@polysoude.comWebsite:
www.polysoude.comRecommended
practice for
inspection of
weld corrosion
ESR Technology has announced that HOIS,
its joint industry project concerning improved
non-destructive testing in the oil and gas
industry, has published a Recommended
Practice Guide for the Inspection of Weld
Corrosion.
This recommended practice document
is the result of a research project funded
by HOIS to provide the oil and gas industry
with guidance on the inspection of weld
corrosion where there are currently no
international standards or recommended
best practices.
The document has been produced to
present a unified recommended practice for
the in-service inspection of weld corrosion
in carbon steel components.
“The publication of this document
provides a recommended practice to oil and
gas producing companies and inspection
companies on the preferred inspection
methods and techniques for a variety of
conditions,” said Dr Steve Burch, ESR
Technology’s head of inspection technology
and HOIS manager. “Increasing our
understanding of asset condition leads to
improved safety, increased efficiencies and
reduced costs”.
The document is available to the entire
industry and can be obtained by registering
and downloading a free copy from the HOIS
section of the ESR Technology website:
www.esrtechnology.com/hois/publicationsESR Technology provides independent
technical expertise, products and services
to help customers ensure asset integrity,
improve reliability, manage safety and risk
and transfer best practice. The company
was previously the engineering, safety and
risk division of AEA Technology, which was
formed from the commercial arm of the
United Kingdom Atomic Energy Authority.
ESR Technology also hosts five
internationally renowned Centres of
Excellence: the National Centre of Tribology,
the National Non-Destructive Testing Centre,
the European Space Tribology Laboratory,
the Pump Centre, and HOIS.
ESR Technology Ltd
– UK
Fax: +44 1925 843500
Email:
info@esrtechnology.comEmail:
steve.burch@esrtechnology.comWebsite:
www.esrtechnology.com