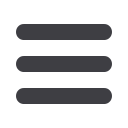

W
elding
T
echnology
100
M
ay
2010
www.read-tpt.com›
THE purpose of a pipeline is to transport
media from one place to another. In this
type of a pipeline only a few pieces are
required: threaded joints in smaller pipelines
and flange joints in bigger pipelines, unless
the pipes are welded. But most pipelines
have further purposes in addition to merely
transporting media. Pipelines distribute
media from feeder point to several locations
or reversely collect media from several
feeder points to collection locations. A
pipeline built for distributing/collecting media
differs from a pipeline built for transporting
media by one critical tubular part – a tee.
There are several types of tees according
to different usage purposes and standards.
With the use of a tee the aim is to create
a situation at the installation on-site where
joining the pipeline’s distributing part would
correspond to joining it to a straight pipe
with different joining techniques.
The requirements set by the usage
purpose define the material and surface
quality requirements of tees in addition
to joining techniques. Particularly in the
food, pharmaceutical and semi-conductor
Welding pipelines, tubular parts and fittings
industries the surface quality requirements
are such that tee-joints made on-site do not
fulfil these requirements. For these reasons
tees have become industrial products and
commercial goods.
A common problem for all manufacturers
is the geometry of the joining point of
two tubular parts. This joining point turns
into a continuously changing arc, which
follows the surface of the main pipe. The
arc of cutting branch pipe is identical to
the arc of the main pipe. These arcs joined
together form the joining surface which is
to be welded. In addition to continuously
changing arc the joining point of pieces to
be welded form an angle which changes
between 0-90 degrees. Controlling the full
penetration of the weld and smoothness of
the inner surface is difficult, causing lots of
expensive after-work.
In order to eliminate the welding and
after-work problem, several pipe branching
methods have been developed where a
collar is formed to the branch’s joining
point and in this way the branch location
resembles the end of a straight pipe. This
type of joint is easily welded manually
and for this kind of welding there are
several good orbital welders, which produce
qualitative results on-site.
As the pipe diameters get smaller and
the wall thickness in relation to pipe’s
diameter grows (becomes thicker) there
are no working collaring methods (for
branching) available. For manufacturing
this kind of “small” tee a new welding
method has been developed by Lacol Ltd.
This welding method is named Larikka
CylinWeld. Larikka CylinWeld is excellent
for manufacturing tubular parts.
Joining the surfaces of two round parts
forms a mathematical pattern and the
simplest approach is from inside and on the
central line of either tubular part. Larikka
CylinWeld utilises the TIG-welding method
and the welding takes place inside the
tubular part. The welding process is fully
automatic and the inner surface quality of
the weld area is smooth. This result is
achieved from the light arc travelling over
the sharp corners of the joining point as
the corners melt forming a round corner.
Further, the root is on the part’s outer
surface making the visual check of full
penetration of the weld simple.
Larikka CylinWeld is also very suitable
for the welding of collared and straight
seams. Larikka CylinWeld is applicable
for the welding of single parts where the
part rotates and the welding is down-hand
welding, which is theoretically the best
welding situation. However, with Larikka
CylinWeld it is also possible to weld long
manifolds. Equipment’s functions can be
applied so that the pipe is stationary and
the electrode rotates inside the pipe. The
operating range of Larikka CylinWeld is
wide with the smallest diameter being 4mm
and the largest 200mm, and in special
cases it can be even larger.
LACOL Ltd
– Finland
Fax: +358 2071 21449
Email:
maarit.aalto@lacol.comRITMO SpA, a manufacturer of welders and
accessories for plastic pipes, has launched
ALFATEL-800, a workshop machine designed
to weld pre-insulated district HDPE pipes and
valves for both heating and cooling lines.
ALFA TEL-800 produces pre-insulated
HDPE elbows within the 400-800mm
diameter range, and jackets for valves within
the 400-710mm diameter range.
District heating is an efficient and low-
environmental impact system for distributing
heat generated in a centralised location
for residential, commercial and industrial
heating requirements. Heat is distributed to
the customer via a network of insulated steel
pipes under pressure. An insulating foam
Welding pre-insulated district
HDPE pipes and valves
wrapped around the pipe minimises heat
dispersion, and the external HDPE jacket
protects the lines.
ALFA TEL-800 has a machine body
with facer and interchangeable heating
elements. The fitting segments are loaded
onto the machine carriages and tightened
by clamps. The hydraulic movements of
carriages, heating element, facer and
clamps are driven by a handy control
panel.
Ritmo SpA
– Italy
Fax: +39 049 9901993
Email:
info@ritmo.itWebsite:
www.ritmo.it