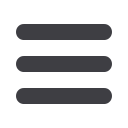

Техническая статья
102
март 2013 г.
www.read-eurowire.com▲
▲
Рисунок 4.
Номинальные коэффициенты расширения
Стенка (д.)
% объема воздуха
Номинальное расширение при толщине стенки
Колебание (6 SDEV)
Тип устройства
впрыскивания
Поток азота (в кубических
сантиметрах в минуту)
Фактическое емкостное
сопротивление (пФ/фут)
Предполагаемое емкостное
сопротивление
▲
▲
Рисунок 5.
Расход газа и колебание емкостного сопротивления
Неспособность
вспенить
материал,
основанный на концентрате в большей
степени
будет
иметь
негативные
последствия при других конструкциях
кабеля.
Для
получения
аналогичных
электрических характеристик толщина
стенки
должна
быть
увеличена,
чтобы компенсировать более низкое
содержание пустот, тем самымпотребляя
больше фторполимерного материала.
Например,
для
вышеупомянутого
одножильного образца неспособность
вспенивания
до
нужной
степени
приведет
к
увеличению
расхода
материала
для
достижения
эквивалентного
сопротивления
примерно на 20% при необходимых 1000
футах на каждый одножильный кабель.
Выбор профиля
смолы
Как только необходимые электрические
характеристики
определены,
выбор смолы заключается в отборе
смолы
на
основе
необходимого
проводника, размере стенки изоляции
и производительности при горении.
Как правило, чем ниже показатель
текучести
расплава,
тем
лучше
производительность при горении (то
есть меньше образование дыма).
Чем выше скорость текучести расплава,
тем больше подходит смола для
более тонких изоляционных стенок и
небольших кабельных конструкций. В
таблице 2 приводятся некоторые общие
рекомендации по выбору смол.
Технологические
параметры и эффекты
– коэффициент
вспенивания
Нередко
кабельные
инженеры
производятрасчетскоростирасширения
для получения низкой теоретической
стоимости. Тем не менее, существуют
и другие важные факторы, влияющие
на стоимость, такие как: техническая
способность,
общие
электрические
характеристики, а также повреждение
и сжатие кабеля после процесса
экструзии.
Пренебрежение
этими
факторами
проектирования
может
привести к ошибочно увеличенной
цене и к образованию большого
количества металлоотходов. Рассмотрим
стандартныйвидеокоаксиальныйкабель,
спроектированный при использовании
59% коэффициента расширения, и
сравним его с аналогичным кабелем, с
54% расширения.
Кабель
с
59%
коэффициентом
расширения может довести процесс
до предела, в дальнейшем увеличивая
первоначальный объем металлоотходов
и приводя к большим технологическим
изменениям.
Из электрических соображений большое
содержание
пустот,
как
правило,
приводит к клеткам большего размера и
к формированию большего количества
клеток вокруг центральногопроводника,
что
может
оказать
существенное
влияние на оптические потери в кабеле
на отражение.
При другом подходе, тот же самый
кабель может иметь коэффициент
расширения 54% с увеличением массы
всего лишь на 0,28 фунтов/1000 футов.
Это небольшое изменение обеспечит
продукции
надежные,
устойчивые
характеристики, меньшие оптические
потери в кабеле на отражение и более
высокую производительность с тем же
самым сопротивлением.
На рисунке 4 приводятся общие
рекомендации
по
увеличению
пенного коэффициента в зависимости
от
толщины
стенки
диэлектрика.
Фактическое максимальное значение
скорости расширения будет меняться в
зависимости от выбора смолы и методов
обработки.
Закачка азота под
высоким давлением
Вспенивание
достигается
путем
подачи
газообразного
азота
под
высоким давлением в расплавленный
полимер
в
процессе
экструзии.
Скорость вспенивания определяется
соотношением
расхода
газа
к
формированию
смолы
при
функционирующем
вращении
экструдера.
Чем больше соотношение расхода газа
к формированию смолы, тем выше
скорость расширения.
Постоянство
потока
газа
имеет
решающее значение для поддержания
равномерной скорости расширения,