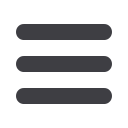

January 2016
MODERN MINING
49
DIAMONDS
Top projects
The high-capacity batch
plant serving both the verti-
cal shafts and the decline. It
has a capacity of 110 m
3
/h.
The Venetia site in October
2015, with headgear erec-
tion at an advanced stage
(photo: De Beers).
system,” he continues. “The facility repre-
sents a major investment by Murray & Roberts
Cementation but a very necessary one, as the
intention is that all the company’s future shaft-
sinking contracts – and not just Venetia – will
be executed using the methodology.”
In terms of equipment, the new system
involves the use of ‘sling down’ jumbo drill rigs
and vertical shaft muckers (VSMs) accommo-
dated in the sinking stage. The sling-down rigs,
apart from dramatically reducing the number
of workers required on the shaft floor during
drilling, offer greater drilling precision than the
jumbo rigs used in the past. As for the VSMs,
they are equipped with long, extendable booms
with jaws on the end and are operated from the
stage in a remote-controlled manner. They will
clean the shaft floor faster and more effectively
than conventional cactus grabs, at the same
time providing far greater safety. The VSMs are
also able to manoeuvre the kibbles – which can
weigh a ton or more – into position, eliminating
the potentially dangerous practice of handling
them manually.
Both the drill rigs and the VSMs being
used at Venetia were originally developed by
a Canadian company, MTI, now part of Joy
Global. Each shaft at Venetia will be served by
two sling-down rigs and two VSMs and these
have already been delivered to site by Joy
Global. A further VSM is in use at Bentley Park.
Delivery of explosives has also changed in
the new method, with pumpable bulk emul-
sions being used – a more efficient way of
charging holes than the stick-type explosives
previously employed. It is expected that the