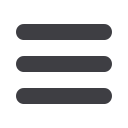

May 2015
MODERN MINING
57
CRUSHING, SCREENING
AND MILLING
feature
P
roducts in the FLSmidth screen
media range include woven wire
screens, modular polyurethane and
rubber screening panels, polyure-
thane and rubber screening bolt
down panels and tension mats, wedge wire
products and wire conveyor belts.
Screen media comprise a relatively small
proportion of the total cost of a plant but play
a critical role in productivity. It is therefore
vitally important that mining operations not
only ensure that they have the correct screen
media in place but that the products used
match the overall system. “FLSmidth has the
necessary expertise to look at a total processing
operation to see where improvements can be
made. From the screen media side, we can look
at any issues related to the process including
wear, mass reduction as well as improvements
in open-area percentage and machine opera-
tion so as to increase the operational efficiency,
throughput and lower the cost per tonne,”
Sibley explains.
“The open area, or the ratio of apertures to
the total panel surface area, is of crucial impor-
tance to screen users at a time when plants are
upgrading their capacity to increase profitabil-
ity and maximise screen performance,” Sibley
continues. “FLSmidth’s modular panels are
among the highest open area screen panels on
the market at present. These combine all the
advantages of reduced mass, high mechanical
strength and longer wear life of polyurethane
with a high open area percentage.”
Modular panels are available in plain poly-
urethane and rubber with additional hybrids
listed as Poly Wedge, Poly Wire and Poly Perf.
Looking at fastening systems, Sibley says
FLSmidth has enjoyed great success with its
patented Bolted Pin System (BPS), a modular
polyurethane screening surface designed to
meet the current and future needs of the screen
media industry. The grom-
mets of the fastening system
comprise a mushroom-shaped
bush that is spigoted onto
the top frame of the disc and
securely L-bolted into posi-
tion, thereby becoming an
integral part of the frame.
The pane l i s l a t ched
securely to the frame, allowing
for high g-forces during opera-
tion of the machine. “This
‘bolted’ assembly negates the
need for the over-size pins or
sleeves whilst preventing the
panel from ‘jumping’ out dur-
ing normal operations which
can be common with the tra-
ditional pin systems,” Sibley
says.
FLSmidth has a range of
woven wire screening which
it claims is the most versa-
tile and common screening
medium in the mining and
aggregates industry. Sibley
explains that there are two
types of woven wire screen-
ing available from FLSmidth.
Woven wire screens are manu-
factured from Vibro Optimax™
wire, AISI 304, 316, BMS and
GMS, while woven wire mesh
is commonly manufactured from AISI 304, 316
and BMS.
“Our woven wire screens are manufactured
from stainless steels, Vibro Optimax™ and
other exotic materials. These round wires are
woven into a weave pattern, with transverse
wires holding the wires together to provide
an excellent open area for peak performance,”
Sibley says. The main benefit of this type of
Careful
screen media selection
can reduce the
‘cost per tonne’
Ludowici reflux classifiers with nozzles.
Stringer cleats which are used with Meshcape™
polyurethane screen decks.
Meshcape™ perforation plates.
FLSmidth has a range of screen media and related products designed to increase throughput and
product quality in the South African mining industry. “Lower commodity prices have meant that min-
ing operations have had to increase their output in order to boost their bottom line or increase life
and maintenance of engineered consumable products to reduce the ‘cost per tonne’ of the process.
One of the ways of doing this is to look at screen media and their impact on production,” says David
Sibley, General Manager: Screen Media, FLSmidth.