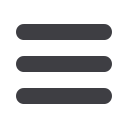

10
M
AY
2016
I NDUS T RY
AHC’s new plant in China
DUTCH industrial company Aalberts
Industries has operated a plant for
surface treatment of components near
Shanghai, China, for around two years,
under the name Hangzhou AHC Surface
Treatment Technology Co, Ltd. Since
1 January 2016, this plant has been
officially integrated into the AHC Group,
which is itself part of Aalberts Industries
NV.
The AHC Group, with its headquarters
in Germany, focuses on providing
technically functional coatings of
surfaces as a service. AHC Hangzhou
can draw on over 50 years of coating
experience within the AHC Group. The
AHC group finishes around one billion
components annually for thousands
of customers in all key industries.
Overall, more than 40
processes and more than
100 process variations
are used, in more than 20
plants for close proximity
to customers.
At
the
Hangzhou
plant, the concept of
sustainable environmental
protection and energy
efficiency meets stringent
Chinese
requirements.
Reproducible and robust
processes are necessary in order to be
able to control the high differentiation of
finishing of customer components.
For this reason, AHC’s process
experience was used in the design of
the coating systems and the wastewater
technology.
AHC supplies surface coatings for
mechanical engineering, and for large
system suppliers to the automotive
industry. Fuel pump casings, impellers
for turbochargers and control pistons for
automatic transmissions, all made from
aluminium alloys, are protected against
wear and corrosion.
The team at AHC Hangzhou provides
different processes of anodisation
and hard anodisation, as well as
electroless nickel plating of aluminium
components. In addition, non-ferrous
metals and ferrous materials, including
stainless steels, are treated with diverse
electroless nickel processes.
Components of up to 1,000kg and
with dimensions up to 3,000mm length
x 600mm width x 1,200mm height
are treated in the anodising line.
Processes are hard anodising Hart-
Coat
®
, Hart Coat GLATT (HC-GL), and
technical anodising, in each case with
the possibility of black colouring and
repressing.
Components
suitable
for
the
electroless nickel plant have a maximum
weight of 1,500kg and maximum
dimensions of 1,100mm x 600mm x
1,500mm.
In addition to the Durni-Coat
®
process,
a variant with incorporated PTFE (PTFE
DURNI-DISP) is offered. This is a dry
lubricant layer having good adhesive
wear properties.
Hangzhou AHC Surface Treatment
Technology Co, Ltd
– China
Email:
info@ahc-china.comWebsite:
www.ahc-china.comAHC Oberflächentechnik GmbH
–
Germany
Fax: +49 2237 502 369
Website:
www.ahc-surface.comDurni-Coat process electroless nickel
coated ball valves
The Hart-Coat system is fully automated and offers series
production reliability
Fives/Salzgitter Mannesmann agree second
tube straightener contract
FIVES has announced that a further
contract has been signed between its
UK-based entity, Fives Bronx Limited,
and Salzgitter Mannesmann Stainless
Tubes France, in Montbard.
This second contract is for the supply of
a six-roll 6.CR9.S straightening machine,
complete with ancillary electrical and
hydraulic control systems and, like the first
Bronx machine ordered in August of last
year, it has been purchased to process
high-yield, thick-wall stainless steel tubes.
Jon Dunn, managing director at Fives
Bronx Limited, said: “The contract has
beenawarded toBronx as a consequence
of the excellent working relationship that
has developed between the client and
ourselves over the past twelve months,
but in particular since the initial contract
was awarded to us last September.
“It is a credit to all UK personnel
involved with the project to enable
the client to have the confidence to
purchase a second machine from us,
without yet having taken delivery of the
first project.”
The equipment is to be delivered
in early-August 2016 and installation
and start-up will be undertaken during
the summer shutdown alongside the
6CR10-HD installation.
Fives Bronx Ltd
– UK
Email:
fivesbronxuk-sales@fivesgroup.comWebsite:
www.fivesgroup.com