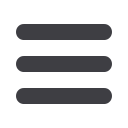

140
S
eptember
2011
www.read-tpt.com›
W
elding
E
quipment
Orbital welding carriage increases production
GULLCO’s Pipe Kat
®
automated pipe
welding system with integrated wire feeder
unit incorporates 40 IPM welding carriage
design with quick action mounting for ease
of installation.
The carriage is equipped with a high
speed return feature for faster repositioning
of the carriage.
The Pipe Kat is also equipped with a
linear oscillator with adjustable weave width
and weld joint centreline adjustment, and all
electronic motorised functions incorporate
jog settings.
The system includes a main control box
with 7,620mm (25ft) umbilical, wire feed
spool capacity of 4.5kg (10lb), maximum
wire speed of 89 to 226cm/min (35 to
633 IPM), and a wire size range of 0.8
to 2mm. The welding torch uses standard
consumables.
Gullco International Limited
– Canada
Fax: +1 905 953 4138
Email:
sales@gullco.comWebsite:
www.gullco.comPipe Kat
automated pipe
welding system
Titanium tube mills
THERE is a very strong trend for production
of seam welded titanium tubes in the tube
market. Titanium tubes are used in airline
engines or frames, chemical and nuclear
power plants as they are very high in
corrosion resistance, light in weight and
high in strength. For each nuclear power
plant a volume of 300 tons of titanium tube
is required. So there is a lack of titanium
tube production capacity at the moment.
The raw material costs of titanium are 10
to 20 times higher than comparable steels.
State-of-the-art is that stainless tube mills
are not able to combine highest tube quality
levels, production reliability and sufficient
production speeds at lowest scrap rates for
titanium tube manufacturing.
To follow this Rosendahl has developed
the new Titanium Tube Mill Series TH-G Ti.
These mills are designed for the production
of tubes for high security relevant issues
like heat exchanger products for power
generation. The main process steps are fully
reengineered according to titanium alloys
properties and end user requirements:
• Tube forming and calibration to handle
high spring back and secure smooth
surface
• Welding and heat treating processes
which can avoid restrictively absorption
of atmospheric gases which would lead
to material embrittlement and corrosion.
The dimension range for the TH-G Ti
Series goes up to 120mm in diameter and
can cover wall thickness values between
0.2 and 3mm.
The unique features of the TH-G Ti
Series are: Rosendahl Hybrid-Forming
for titanium tube production combines the
advantages of moveable and non-moveable
tooling; introduction of high performance
level to the titanium tube manufacturing
by use of high-end TIG-plasma- or laser
welding technology; fully integrated quality
control system including continuous
thermographical analysis of the welding
seam; STOP and GO production for zero
defect welding for minimisation of scrap
rates; and Rosendahl titanium tube mills
are equipped with in-line annealing systems
which can also handle the speed range
achievable with Laser Welding Systems.
Rosendahl Maschinen GmbH
– Austria
Email:
office@rosendahlaustria.comWebsite:
www.rosendahlaustria.com