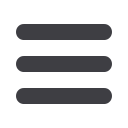

S
eptember
2011
143
›
W
elding
E
quipment
Quality-control methods for manufacturing
welded tube and pipe
HIGH frequency resistance welding (HFRW),
also referred to as electric resistance
welding (ERW), is a major process used
in the production of welded tube and pipe.
HFRW mills operate at very high speeds,
generally ranging from 50 to 500ft per
minute, depending on material diameter
and thickness. Application sizes range from
hypodermic needles to pipelines. A wide
range of commonly used metals can be
welded, including low-carbon and alloy
steels, ferritic and austenitic stainless steel,
and many aluminium, copper, titanium and
nickel alloys.
In this continuous process, high-
frequency current is concentrated in the
formed strip edges and generates rapid
heating in a small volume of metal at the
weld interface. Pressure rolls are then used
to force the edges together to produce a
welded tube or pipe.
Although the quality of the weld can
be very high, a few weld-related quality
problems exist. Modern non-destructive
techniques such as eddy current and
ultrasonic inspection are commonly used
to detect open seam conditions such as
cracks. However, the major problem that
remains undetected is a condition referred
to as cold weld (also called paste or stack
weld) that is the result of improper welding
parameters. Today’s inspection and non-
destructive evaluation (NDE) techniques are
not able to detect the cold weld condition.
This condition is difficult to detect because
it appears visually and metallurgically to be
a good weld. A cold weld is usually welding
process-related, and is typically revealed
during mechanical testing or in service as a
fracture or splitting along the weld seam.
The EWI tube and pipe mill team is
applying new quality-control methodologies
and monitoring techniques to HFRW
mills, resulting in significant reduction and
eliminating weld quality problems related
to premature weld seam failures due to a
cold weld condition. Understanding the weld
process variables and their relationship to the
final weld characteristics and properties is key
to the methodology developed by EWI. Full-
scale testing and portable instrumentation
capabilities at EWI are extensively supporting
the tube and pipe mill projects.
In-plant experimental techniques have
been developed and refined to generate
production mill process windows for a
range of critical welding variables such as
temperature, squeeze force, displacement
and mill speed. Monitoring the welding
parameters can be completed with traditional
data acquisition sensors and systems.
Monitoring the resultant weld seam shape,
size and characteristics is performed using
a non-contact optical technology. This
technology uses commonly available laser
sensors to make measurements of the
surface profile of the pre-welded and just-
welded tube surface. These profile images
are compiled from three-dimensional surface
topography data.
Edison Welding Institute
– USA
Email:
mkimchi@ewi.orgWebsite:
www.ewi.orgT
+31 321 38 66 77 |
F
+31 321 31 41 65 |
info@magnatech-international.com•
AUTOMATIC PIPE
WELDING SYSTEMS AND
RELATED EQUIPMENT
• FROM 6MM AND UP
• INTERNAL/EXTERNAL
WELDING
PROCESSES:
GTAW
GMAW
FCAW
www.magnaTech-InTeRnaTIOnaL.cOmCOMPANIES WHO
BELIEVED IN
a PaRTneRShIP
wITh US:
ROYAL DUTCH SHELL
KELLOGS BROWN AND ROOT, USA
NORSK HYDRO, NORWEGIA
HEEREMAC, THE NETHERLANDS
FMQ, SAUDI ARABIA
QUALITY INTERNATIONAL, UAE
FLUOR DANIEL SADA, USA
CCIC, QATAR
SUEDROHRBAU, SAUDI ARABIA
STORK MEC, BELGIUM
NACAP ASIA PACIFIC, THAILAND
EXXON MOBIL, USA
OILSERV, NIGERIA
GENERAL ELECTRIC, USA
TEKFEN INSAAT, TURKEY
MONTER STROJARSKE MONTAZE, CROATIA
GALFAR E&C, OMAN
ARAMCO SERVICES, SAUDI ARABIA
CANADOIL ASIA, THAILAND
VAM, MCE GROUP, AUSTRIA
OAO LUKOIL, RUSSIA
LARSEN & TOUBRO LTD, INDIA
NIS-NAFTAGAS, SERBIA
PETROJET, EGYPT
KEVIEPSZER KFT., HUNGARY
KVV ZRT., HUNGARY
PETROFAC, UAE
ENI-SNAM, SAUDI ARABIA
BIN QURAYA EST, SAUDI ARABIA
and many mORe...
MA09185_MAGNATECH_ADV_118x190.indd 1
29-01-2009 15:30:32