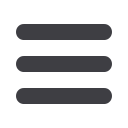

Wire & Cable ASIA – September/October 2007
127
www.read-wca.com12
This technique is done offline where the line speed is
slower or zero. This process is very tedious and time
consuming; so it is usually for customers who require this
type of inspection. As print legends can be lengthy, there
is a high chance of human error during the inspection.
Also, the threshold of each operator is different and print
quality is judged differently.
2.3 Image Capture and Sampling
This process involves a camera acquiring an image based
on an encoder signal and sampling rate. The image is then
shown on a display for the operator to process a sample
of images to determine if there are any print defects.
Some main limitations are fatigue, operator’s thresholds,
and slower processing speed. There is also a chance of
missing some print defects depending on the sampling
rate.
3 Machine Vision Inspection System
3.1 Optical Mechanical Design
The print verification system (
Figure 1
) consists of a
camera and adequate lighting to capture images of
print legend moving at speeds more than 1,400ft (460m)
per minute.
Multi-camera systems may be needed to handle cables
with several print legends. For example, wires with print
legends on opposite sides require a two-camera system.
The camera and lens provide a field of view to cover the
print legend (
Figure 2
). Image capture is synchronised
with the printer and line speed. The image will be used
for further software processing. The lighting can vary
depending on the application. The factors in consideration
are the reflectivity of the material, surface profile, colour,
line speed, and lens aperture.
To ensure consistency in the images, the setup features
an enclosure to prevent other lighting, dust particles, and
other factors from affecting the results. Vibration of the
cable is also minimised by wire guides to prevent images
from being out of focus.
One other challenge is the location of the PV system and
to ensure the print stays within the camera’s field of view.
The recommended location for the PV system is directly
after the printer, where the print will be in the correct spot
consistently. Placing the PV system further down the line
will result in a high chance of cable twist, which causes the
print to be anywhere around the cable and outside the field
of view.
3.2 Software
Advance algorithm is used to process the images for print
defects inspection. There are a number of algorithms: print
quality detection, optical character verification (OCV), and
optical character recognition (OCR). Different algorithms
are implemented depending on the requirements and
budget.
For print quality detection, it utilises a method called
pattern matching. This method requires a template of
a good print on that specific cable. The template is
compared to each captured image during a run. If the
two images differ beyond the desired threshold, an alarm
will notify the operator and an error report is saved to the
ongoing data log. The print defect will also show up on the
display for operators to clarify.
OCV and OCR algorithms are more complex and are an
extension to the pattern matching technique. For OCV,
the software will verify each letter of the print legend.
Alphabets of different fonts are stored in the database. The
desired print legend is broken down into individual letters
of the same font. Each captured image is also broken
down into individual letters. Each letter will be compared
to the desired letter. If there are differences beyond the
threshold, it is a print defect. However, the software does
not know what the misprinted letter is.
OCR is the most advanced. The algorithm is very similar
to what an operator would be able to detect with the eyes
and mind. Not only would the software find out if a letter is
different from the desired print legend, but it will be able
to recognise the misprinted letter(s). This helps identify
exactly what the mistake is and immediate actions to fix
the system can be done.
3.3 Improving Quality Assurance
Suitable for any Type of Products
Since the PV system uses machine vision, it
is able to inspect the print legend for any type
of products. With proper set-up of the optical
components, the system can be used on bare
wire, cables, pipe, tube, tapes, flat sheets, etc.
Suitable for any Type of Printers/Fonts
The PV system uses image templates as a
reference. The reference fonts or print legends
are predefined at the start-up. Regardless if
the print legend or fonts are done by an inkjet,
inkwheel, hot foil or laser printer, the software
will be able to compare the print legends to the
references.
Reduce Defects On-The-Fly
The PV system provides the operator with a
view of the current print legend as well as the
most recent print defects. This continuous
stream of real time information – especially
failure data – allows the operator to isolate the
causes of print defects while the production
❍
❍
Figure 2
: Print View System Overview
Alarm
Cable
Direction
Camera
Software
Display
Lighting