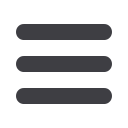

Wire & Cable ASIA – September/October 2007
128
12
www.read-wca.com3.5 Test Results
Taymer’s Print Verification System has been tested in the
industry extensively on different products, print messages,
and using types of printing methods.
The two authors worked closely with Commscope in
Claremont to bring this QA technology to the plant. The
before and after print defect data was recorded. After one
year of use, print defects were reduced by over 50%.
The reasons were as follows:
• Minor print quality issues were caught before they
became an actual defect. For example the operator
adjusted the printer or fixed cable alignment
• Printer maintenance was initiated before the printer
actually malfunctioned because the operators received
very current feedback on print quality
• Incorrect print legend was identified before the entire
run was misprinted
3.6 Sample Images
Figures 3-5
are sample images or screenshots of print
defects found by the PV optical system on different
products.
Conclusions
With a Print Verification System, the print legends on the
cable can be inspected thoroughly for defects. The system
provides several benefits:
• Suitable for any type of products – wire/cable/hose/
pipes/bars/plates/stranded product
• Suitable for any type of printers – inkjet, ink wheel, hot
foil, laser, indent/emboss
• Ensure the customer will not get defective products,
improving customer relationship and confidence
• Reduce reprinting and eliminate consumable waste
resulting in material cost and labour cost
• Assist in internal improvement to production process to
reduce defects
Acknowledgments
Special thanks also to the IWCS staff for making this
template available for this year’s publication.
line is still running. If the print quality is degrading below
the threshold, the operator can immediately adjust the
printer to improve the quality. Also, operators can use
the PV system at the beginning of the run to set-up the
printer and check to ensure the print legend is correct. The
PV system allows changes to be made on the fly, greatly
reducing reprint of the cable post production.
Quality Assurance
The system will capture images of the printed cable at high
line speeds, and save the images of the print defects to
disk for use in quality reports.
The PV system’s display makes it easy for engineering
and production supervisors to examine the defect without
having to see the defect itself. Defect locations are
recorded together with the image allowing for easy report
generation and further analysis.
3.4 Limitations
There are a few limitations to the print verification system.
• For different types of cable surface (round/twisted
profile), and fonts, the same print legend may look
different. Therefore, different templates are required for
different types of cables
• Lengthy print legend can also twist out of the camera
view, resulting in missing characters. There is a high
chance of this happening on twisted pair wires
• Since the camera is looking at the surface, water
droplets/grease/dust particles would show up
affecting the print legend resulting in false defects.
To compensate for them, the system would need
to decrease the quality threshold or an air wipe is
necessary
Craig Girdwood
Taymer International Inc
145 Renfrew Drive
Markham
Ontario
Canada L3R 9R6
Tel
: +1 905 479 2614
:
craig.girdwood@taymer.comWebsite
:
www.taymer.comBrian Franklin
Commscope
Claremont
North Carolina, USA
Tel
: +1 828 324 2200
:
info@commscope.comWebsite
:
www.commscope.com❍
❍
Figure 3
: Missing print detected at 900ft/min
❍
❍
Figure 5
: Screenshot of print quality comparison
❍
❍
Figure 4
: Poor print quality detection at 200ft/min