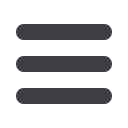

April 2015
MODERN MINING
35
feature
COUNTRY FOCUS –
ZAMBIA
Kagem carries the flag
Kagem, which has three rivers (including the Kafue and the Kafubu) on
its boundaries, is located in the central part of the Ndola Rural Emerald
Restricted Area (NRERA). The discovery of beryl (emeralds are a gemstone
variant of beryl) in the area dates back to 1928 although mining of emeralds
on any significant scale apparently only began in the 1970s.
The Kagem mine is one of only three sizeable mines in the area but the
NRERA also hosts several hundred informal miners. Kagem is by far the big-
gest producer and has been described by the Zambian government as “the
flag-bearer company of the Zambian gemstone industry.”
Chisel men at work watched by security personnel.
A Cat 336D excavator loads a Cat 730C ADT. Kagem’s mining fleet is modern and well
maintained.
from a few centimetres up to 2 m in thick-
ness, are what we target – everything else is
waste,” he said. “In the Chama pit, the TMS
dips at 16 deg to the south and south-east and
is cross cut by the pegmatites vertically. The pit
slowly migrates as we follow the TMS and, in
fact, we’re now busy with our fourth highwall
pushback, which will extend the pit by a fur-
ther 75 m to the south-east.”
He pointed out that the emeralds that form
within the ore (reaction zone) tended to occur
in pockets. “The result is that you have good
times and bad times – but they tend to even
out,” he noted. Grade can vary considerably
but averages out to 300 carats per tonne for the
Chama pit.
Gessner added that most of the rock han-
dling in the pit related to the waste with ore
production only accounting for about 8 000
tonnes a month. “The waste stripping is a 24/7
operation carried out both in-house and with
the assistance of a contractor whereas we do
the ore mining ourselves and only during day-
light hours – because we need good visibility
to detect the emeralds, which are normally
encrusted with schist, and for security reasons.
Although excavators are used to open up the
contact zone, essentially this is a manual oper-
ation by teams of chisel men – watched over
by security personnel and geologists – who
recover the exposed emerald crystals, which
are then placed into lockable production boxes
and taken to the sorting house. The balance of
the material in the contact zone is loaded into
ADTs and taken to the processing plant for
recovery of emeralds – and beryl – not detected
by the hand mining.”
A strip-and-fill mining method is used by
Kagem. This involves stripping the high wall
and filling in the exhausted footwall with the
hard rock, which contains the size of the pit
and keeps the environmental liability under
control. Stripping ratios are enormous com-
pared to conventional mines and are currently
varying between 80 and 100 to 1 as a result of
increased contractor stripping.
While the mining operation at Kagem
is huge and quite complex, the processing
operation – which is chemical-free – is very
straightforward, involving ore crushing and
washing followed by screening in a triple-deck
unit, after which the material reports to a pick-
ing belt facility where the emerald crystals are
picked out by hand from a series of picking
belts. The picking operation goes on around
the clock in three eight-hour shifts, with lower
quality material being processed at night. The
final part of the process involves the cleaning
and grading of the emeralds in the sort house
and their assembly into parcels for auction.
Interestingly, the management at Kagem is
mainly composed of Indian expatriates, headed
by C V Suresh, who is Director of Operations.
The total number of expats is currently 59 but,