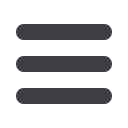

32
MODERN MINING
April 2015
feature
COUNTRY FOCUS –
ZAMBIA
T
he first thing that the visitor notes
on entering the mining area at
Kagem is the sheer size of the op-
eration. Most coloured gemstone
mining around the world tends to
take place on a relatively small scale – often
by informal miners – with mining methods
typically being very labour intensive. Kagem,
by contrast, is highly mechanised – at least
in terms of its stripping and waste removal –
and
Modern Mining
saw an impressive fleet of
modern excavators, articulated dump trucks
and drill rigs operating in the main pit, Chama,
which is now 120 m deep and roughly a kilo-
metre in length. Totalling nearly 100 units if
ancillary equipment is included, the mining
fleet handles nearly a million tonnes of rock
a month (considerably more in some months),
a figure which is dramatically up on the ap-
proximately 125 000 tonnes a month being
achieved when Gemfields acquired Kagem.
Talking to
Modern Mining
from London
in a phone interview, Gemfields’ CEO, Ian
Harebottle, cited the problems that the com-
pany inherited in 2008: “We found a site
with a huge waste removal backlog, no ore
at the pit bottom for production, no effec-
tive security systems, poor health and safety
Kagem –
a thoroughly
modern
gemstone
mine
This panoramic view of the Chama pit gives an idea of the scale of the Kagem operation.
While Zambia is noted for its world-class copper deposits, not so well known is the fact that it now
hosts the world’s largest emerald mine, Kagem, which has been transformed over the past seven
years from an under-funded, inefficient, loss-making operation into one of the success stories of
Zambia’s mining industry. Responsible for the turnaround is London-based, AIM-quoted Gemfields,
which has invested well over US$60 million in the mine since acquiring it in 2008.
Modern Mining’s
Arthur Tassell recently visited the site – located about 60 km to the south of Kitwe on the Copperbelt
– to see for himself the scale of the transformation.