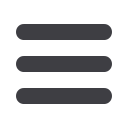

88
J
anuary
2015
Article
Shandong SiFang Technical Development Co Ltd
pipe defect peaks from normal pipe contour effectively
[1, 2]
.
The die-type crimping press has the upper die and the lower
die of the certain working surface curve. As with producing,
the upper die is fixed and the lower die is driven upwards
by hydraulic cylinders, resulting in the margin crimping
deformation of the plate between the upper die and the lower
die. The crimping step number of the whole plate depends
on the length of the dies and the plate. The crimping quality
of the die-type process is superior compared with that of the
roller-type press, especially for high-strength thick-wall pipes,
also avoiding longitudinal extending of plate margins in roller-
type press.
2 Baosteel crimping press and
characteristic of its dies
The crimping press of Baosteel UOE welded pipe production
line consists of two oppositely arranged frameworks, which
can move vis-à-vis depending on the width of the steel
plate, and the upper die and the lower die are installed in
the frameworks. Baosteel crimping press has the following
characteristics:
1) high pressure; its maximum pressure reaches 40MN,
making it possible to produce high steel grade size in the
future; the capacity of great pressure can guarantee the
production requirements of high steel grade and thick wall
size, and also realise the large step operation of crimping
press; as for its length, according to finite element
analysis, the crimping force limit of 31.8mm X100 pipeline
steel will reach 38MN
2) large length of single step; the effective length of its dies
is about 4,900mm; there are only four crimping steps for
completing the pipe of 18m long; the reduction of the step
number means the improvement of production efficiency,
and the reduction of the forming transition zone number so
as to improve the product quality
3) few dies; as for 56" production line, there are only five sets
of dies covering OD 508 ~ 1,422mm.
Forged alloy tool steel dies have been made in Germany
for matching Baosteel 40MN crimping press before, and the
chemical composition is shown in Table 1.
The field test shows that the surface hardness of the die is
50-60 HRC.
The German tool steel, as for the chemical composition,
is equivalent to Chinese Cr12Mo1V1, American D2 and
Japanese SKD11, which is cold working tool steel widely used
internationally; it is ledeburite steel, and has high abrasion
resistance and hardenability, which would be hardenable
completely at less than 300-400mm in cross section. It
is variously used as cold working die, cutting tools and
measuring tools of high precision and long lifespan, such as
punch dies, stretching dies, cut-off dies, cold extrusion dies,
cold cutters, circular saw blades and standard measuring
tools.
The smelting of this kind of steel requires high purity by
electric furnace and vacuum refining furnace, and generally
forging stock of large dies are obtained through the electroslag
remelting system. The forgeable temperature zone is narrow,
exactly speaking, from the starting forging temperature
1000°C to the ending forging temperature 850°C. The upper
die and the lower die are elongated parts, and should be
completed after repeatedly heating and forging; meantime
contour forging is difficult for the small production quantity.
Generally speaking, elongated parts are easy to be stretched
and hard to be upset, resulting in significant anisotropy, whose
mechanical property can vary more than once. Manufacturing
crimping dies of forged die steel brings on process complexity,
high-energy consumption, low material utilisation and high
cost.
The heat treatment of this kind of steel is difficult and
demanding, and the typical curve of heat treatment is shown
in Figure 2.
Original dies are all made in Germany, so if imported, there
would be some trouble, such as long manufacturing cycle,
high cost and fussy purchasing process. Some dies have
been in service for too long, are badly worn, and there are no
C
Si
Mn
P
S
Cr
Mo
V
1.50~
1.60
0.10~
0.40
0.15~
0.45
≤
0.030
≤
0.030
11.0~
12.0
0.60~
0.80
0.90~
1.10
Table 1: Chemical composition of German die steel (mass fraction, %)
Figure 2: Typical curve of heat treatment
lower than 400°C
entrance
entrance
heating
heating
pre-heating
750~800°C
1,010~1,040°C
salt bath (air-cooled)
air-cooled
1 time
high temperature 480~550°C
low temperature 180~200°C
high temperature 480~550°C
low temperature 180~200°C
2 times
(object 1,025°C)
soaking