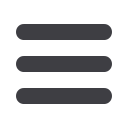

J
anuary
2015
89
Shandong SiFang Technical Development Co Ltd
Article
spares, so Baosteel is urgent to purchase new dies. Due to the
intellectual property protection of the German manufacturer of
the original dies, Baosteel has difficulty getting manufacturing
details. Because of the tiny field of crimping die manufacturing
and manufacturing difficulty, official publication and peer
communication have demonstrated that crimping dies in large
diameter pipe plants have not been manufactured of a similar
material in China. So far the research on crimping processes
has concentrated on crimping width setting under different
pipes and different dies while, as for the die itself, there is
less research on the die manufacturing, including the material
selection and the manufacturing process
[3-6]
.
3 Self-development of
crimping die
After the service condition analysis and research of the
crimping die, neither the chemical composition nor the forging
processing of the original German manufacturer has been
imitated simply, and the cast processing solution of new high
chromium alloy has been developed eventually. The detailed
manufacturing drawings of the dies have been determined
with the original dies through geometrical measurement of
three-coordinates measuring machine and checking of the die
assembly matching of the equipment body.
3.1 Research and development of new high chromium
alloy
High chromium alloy is a material of chemical composition that
offers a wide range of uses; different chemical composition
and heat treatment processing result in distinct microstructure,
hardness and toughness. The development of new material
must been in accordance with the service condition of the
crimping dies.
In high chromium alloys the basic and important alloying
elements are C and Cr, whose content has a decisive effect
on the amount of carbide, the quantity ratio of M
7
C
3
carbide
and total carbide, hardness, toughness and hardenability. The
microhardness of M
7
C
3
carbide is about 1,800HV, while the
microhardness of M
3
C carbide is only about 800HV, therefore
the suitable ratio of Cr/C can result in excellent comprehensive
performance of hardness and toughness.
Element Mo distribution in the phases of high chromium
alloy is about 50 per cent in Mo
2
C, about 25 per cent in M
7
C
3
carbide effective to improve hardness and wearing resistance,
in addition about 23 per cent dissolved in the matrix, which
significantly improves alloy hardenability.
The combination of V and C can generate primary carbide
and afterwards secondary carbide, so that the solid solution
amount of carbon in the matrix will decline and the point Ms
will increase. Certain amounts of V can refine microstructure
during solidification, having a favourable effect on elimination
of bulky columnar grain.
The binding force between W and C atoms is large, improving
martensite stability in high temperature, thereby increasing
red hardness. In hot quenching, partial W carbide dissolves
into the matrix to improve hardenability.
Ni can strengthen the matrix to improve the material
comprehensive performance, and improve hardenability.
Ti can form stable TiC nuclei, and refine eutectic microstructure.
Adding Nb can make the precipitation of high hard Nb
(CN) particles (2,000HV) in the matrix, and these particles
have a high melting point, regular shape, small size and
uniform distribution in the matrix. Therefore, adding Nb can
control the solidification segregation effectively, improving its
comprehensive performance and saving Ni or Cr.
The chemical composition of new high chromium die steel
has been designed based on service condition of crimping
dies and effects of various alloying elements listed in Table 2.
3.2 Research and development of cast form processing
Cast form processing is another key factor to ensure the
die manufacturing quality. The new casting processing and
equipment have been designed according to the crimping
die shape and casting character of new high chromium die
steel. Electrical furnace smelting and refining ensure purity
of molten steel and advisable casting system ensures quick
uniform filling, reducing segregation
effectively.
The developed special device breaks
up initially formed dendrites, and the
small dendrites distribute throughout
the alloy liquid, forming effective
crystal nucleus, which result in fine
uniform equiaxed grains in the cast
dies; meantime, casting defects, such
as shrinkage porosity, are avoided
generating in order to obtain high
quality casting blanks.
C
Si
Mn
P
S
Cr
Ni
Mo
Ti
V
Cu
RE
1.80~
2.80
≤
1.0
≤
1.0
≤
0.05
≤
0.05
12.0~
22.0
0.5~3.0
0.8~
3.0
≤
0.30
≤
1.0
≤
1.0
0.01~
0.5
Table 2: Chemical composition of new high chromium die steel (mass per cent, %)
[7]
Figure 3: Ultrasonic testing results of cast dies (distance-amplitude curve)