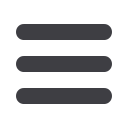

wire
2016 show
➣➢➣
4-8 April
March 2016
134
www.read-eurowire.comAutomatisation
is
an
important
topic, especially for large diameter or
high-tensile wire. The automatisation of
the drawing-in process eases the work of
the operator considerably.
In
addition,
for
higher
e ciency
Kieselstein developed, in cooperation with
an international operating company in the
wire industry, a new soap supply system
which will be presented at the stand in
Düsseldorf.
For increasing the availability of the plant,
IT-based maintenance becomes more
important. Demands for spare parts can
be identi ed correctly, maintenance
measures can be planned and down-time
can be avoided.
A team of specialists in IT, programmable
control and machine engineering works
on this in order to provide tailor-made
solutions to customers.
Kieselstein International GmbH –
Germany
Website
:
www.kieselstein.comErnst Koch
Stand: 10F22
Koch’s presentation will be focused on
highly developed machines and an
innovative acoustic emission analysis for
increasing the quality of products.
The company will have a sophisticated
portfolio of machines and quality-
improving
innovative
processes
on
display. These include a multiple-drawing
line from the KGT series as well as a wire
pay-o and a spooler for the collection of
the wire.
The line produces steel qualities with low
carbon content (0.12%) on a machine
with ve drafts. In actual operation,
the line is then complemented by nine
drawing-blocks and includes high-quality
pre-treatment
of
the
wire.
This
con guration enables a drawing speed of
around 50m/s.
A further highlight at the Koch stand will
be a modern system for the continuous
control of wire quality. Using acoustic
emission analysis, the forming process
during operation is permanently analysed.
Even minor anomalies are detected,
guaranteeing production quality. The
high-level detection of faults, as well as
the increase in manufacturing speed, are
the bene ts of this technology – the use of
which Koch is promoting heavily.
In addition to technical highlights,
for managing director Jochen Koch
value orientation is also crucial for the
company’s international success.
“As a family-run company our work is
more to us than just a business. We put
great emphasis on stable relations that
are based on appreciation, both with our
customers and our members of sta . The
fact that we strongly respect values such
as fairness, reliability and integrity in our
business relations is appreciated by our
customers – and they also bene t, with
high quality and comprehensive service.”
Koch’s portfolio includes single-block
machines and multiple drawing systems
through to cold rolling and stretching
systems. As a supplier with high service
orientation, it plans, delivers and installs
complete lines with all components
necessary for the manufacturing of wire.
Ernst Koch GmbH & Co KG – Germany
Website
:
www.koch-ihmert.deKrenn
Stand: 10G66
With the acquisition of the steel cutter
and testing press division from Kamax
in 2015 the product range of Krenn has
signi cantly expanded.
For the rst time the medium-sized
German company with a tradition of
almost 70 years presents the high-quality
hydraulic Kamax steel cutters. Kamax
hydraulic presses for the compression
testing of wire samples with a maximum
diameter of 45mm and a piston pressure
of 500 to 5,000kN will be introduced.
These are also available as a double press
with integrated cutting device as well as
special designs.
Werkzeugfabrik Albert Krenn eK –
Germany
Website
:
www.krenn.deKurre Group
Stand: 09C49
The Kurre Group has extended its product
range for the wire and cable industry by
establishing another company, Kurre-
Kabelfertigungsmaschinen GmbH.
This has led to expansion with automatic
coil winders, automatic drum winders,
packaging
systems,
and
palletising
systems. This also includes the established
counter series, MW5, MW8 and MW10,
which are licensed to MID-009 and are
exclusive to Kurre-KFM.
The rst project for Kurre-KFM was a
rewinding line with traversing portal
winders for a factory in China.
This rewinding line was designed for a
quality control process for products from
Ø3mm to 60mm and is able to handle
spools from Ø450mm to 1,600mm with a
maximum weight of four tons.
Tension can be applied to the product
either with a dancer unit for products up
to a maximum diameter of 15mm or with
a torque control for products larger than
15mm.
The
automatic
failure
repositioning
system is able place a detected failure on a
de ned position.
▲
A shaving plant from Kieselstein
▲
Technically highly developed machines and
systems for innovative processes are at the centre
of Koch’s presentation
▲
Kamax SK 22 hydraulic steel cutter for the safe
and e ortless cutting of wire and bars