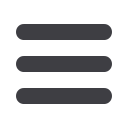

wire
2016 show
➣➢➣
4-8 April
March 2016
156
www.read-eurowire.com➣➢➣
HOSN’s products are all certi ed with
ISO9001 and CE, and can be found in 60
countries worldwide.
HOSN Machinery Technology – China
Website
:
www.hosnglobe.comSiebe Engineering
Stand: 10B22
Siebe Engineering has been o ering
single screw extruders as well as
complete ready-for-use extrusion lines
for automotive cables, building wires,
data-communication cables, special cables
and plastic-tubes for high quality products
to its international customers for more
than 30 years.
These extrusion lines are designed
according to customers’ requirements
and optimised to meet the increasing
demands of the industry for highest
quality, highest productivity and a
minimum of production scrap.
Besides
the
newest
HSP-extruder
technology on display, Siebe will also
demonstrate the latest version of the
unique Siebe Colour Match System, which
detects cable colours inline at line speeds
up to 1,500m/min and more.
Siebe Engineering GmbH – Germany
Website
:
www.siebe.deSikora
Stand: 09A41
At the leading show for the wire and
cable industry, Sikora is presenting a full
programme of well proven and innovative
non-contact
measuring,
control,
inspection and sorting devices for quality
assurance and cost reduction in the wire,
cable, optical bre and plastics industries.
Harry Prunk, a member of the board at
Sikora, said: “I am looking forward to
meeting and talking with customers,
friends and interested show visitors while
introducing our innovative technology.
“This is among others the Preheater 6000
TC, a temperature controlled conductor
preheating device that assures an
optimum adhesion of the PE or other
plastics on the conductor. In this context
we will also present the Wire-Temp 6000,
a non-contact conductor temperature
measurement system that is now also
available for diameters up to 50mm and
suitable for installation in CV lines.
“Another highlight will be the Purity
Scanner for online inspection and
sorting of plastic material that is used,
for example, for the insulation of power
cables. The system assures that only pure
material is entering the extrusion process
and the nal product.
“Furthermore,
the
Purity
Concept
Systems celebrate their premiere. With
this technological innovation there are
modular designed devices available for
on- or o -line inspection and analysis of
pellets, akes and tapes/ lms. The systems
are based on X-ray, infrared or optical
technologies depending on application.
“In addition, visitors will get to know
our sophisticated systems for quality
assurance of optical
bres in the
drawing tower. The product series is
now complemented by a gauge head
for measuring the bre temperature as
well as innovative equipment that gives
information on the coating concentricity.”
Selected technological highlights on the
Sikora stand include:
Preheater 6000 TC
: Temperature controlled
conductor preheater for optimal adhesion
of the insulation
Wire-Temp 6000
: Non-contact temperature
measurement of the conductor
Wire-Temp 6050
: For conductor diameters
up to 50mm
Purity Scanner
: Inspection and sorting
system for XLPE pellets
Dual
inspection
:
X-ray
and
optical
technologies for detection of metallic and
organic contamination from 50µm on the
pellet surface and inside the pellet for
highest material quality
Purity Concept Systems
: Modular designed
systems for on- or o -line inspection
and analysis of pellets, akes and lms/
tapes; based on X-ray, infrared or optical
technologies; detection of contamination
from 50µm
Fiber Series 6000
: Diameter measurement
before and after coating; determination
of the bre position, vibration frequency,
tension and spinning; airline detection;
100 per cent lump detection
Highlight
:
Temperature
measurement
of the optical bre and concentricity
evaluation of the coating
Sikora AG – Germany
Website
:
www.sikora.netSimufact Engineering
Stand: 15D13
Simufact Engineering, an MSC Software
company, will provide insights into recent
enhancements
in
its
manufacturing
simulation
solutions
Simufact.forming
13 and Simufact.welding 5. Simufact has
further extended the elds of application
of its solutions, additionally covering
manufacturing processes such as resistance
spot welding, pressure welding, friction stir
welding, and electrical upsetting.
Both software solutions, Simufact.forming
and Simufact.welding, are well established
simulation solutions employed for the
design and optimisation of manufacturing
processes in metalworking industries. The
solutions cover a wide range of forming
and joining processes including cold
forming. Simufact solutions are employed
in the automotive and aerospace
industry and their respective suppliers, in
mechanical engineering companies and
other industries.
The current version of Simufact.forming
for the simulation of forming processes
comes with improvements in software
stability, accuracy and speed. In terms
of speed the current version cuts down
calculation times signi cantly; sheet
metal forming process simulations can be
processed up to 50 per cent faster.
▲
An extruder from Siebe
▲
The Wire-Temp 6050 is designed for conductor
diameters up to 50mm
▼
simufact.forming from Simufact