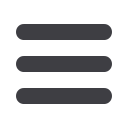

4-8 April
March 2016
153
www.read-eurowire.comwire
2016
show
➣➢➣
CANDOR Sweden AB
Tel: +46 11 21 75 00 Fax: +46 11 12 63 12
Email:
info@candorsweden.comSingle wire plating plant
• Electrolytic plating
• Candojet hot water cleaning
• Electrolytic & Ultrasonic degreasing
• Welding wire cleaning and copper coating
• Pickling & phosphating
Ultrasonic
& Electrolytic
www.candorsweden.comMulti wire cleaning plant
Over the last two years, Nextrom has
focused on further developing its preforms
and bre manufacturing solutions to
attain excellence, allowing customers
to further improve productivity while
reducing production costs: High-yield VAD
core process, OVD cladding technology
with SiCl4 or D4, draw towers for extreme
speeds, very large preforms and spools, and
the recovery of helium, to name just a few.
In the
eld of
bre optic cables,
Rosendahl and Nextrom have not only
worked regularly on achieving further
developments, but also hit the “high
performance” button.
The new “turbo” loose tube line not only
saves space thanks to its new design
and technology, but is also e cient
with regard to material and energy
consumption.
With its product speed of up to 1,000m/
min, it is claimed to represent the fastest
secondary coating line on the market.
Live streams show the lines in production.
In addition, the new ROBI high-speed,
low-tension binder will be presented as
part of the SZ stranding programme for
bre optic cables.
Rosendahl and Nextrom GmbH –
Austria
Website
:
www.rosendahlnextrom.comSaco AEI Polymers
Stand: 11E42
Saco AEI Polymers is a customer-driven
manufacturer providing premium value
and innovative polymer solutions in North
America, Latin America, Europe and MENA.
The company, under the leadership
of Aesse Investments Ltd, focuses on
optimising quality, driving e ciency, and
ultimate value for customers’ products.
The company delivers value to customers
by developing and manufacturing a full
range of thermoplastic and thermoset
compounds,
additives
and
catalyst
master-batches for the wire and cable,
building and construction, pipe and
tubing and speciality markets.
Its expertise and commitment to custom
formulating for unique applications
delivers world-class product solutions,
commercially available o -the-shelf.
The technology portfolios of compounds
are built on industry leading Pexidan®
moisture cure XLPE, Thermodan® HF and
CP LSZH/CPE and Ekopren® EPDM/EPR
resins.
This
expertise
also
extends
into
halogenated
and
non-halogenated
ame-retardants, synergists, and smoke
suppressants for the development of
compounds that meet or exceed the
performance requirements of global
regulatory industry standards.
Saco’s dedication and investment in
research and development has resulted
in fast go-to-market solutions for its
customers. The global R&D facilities are
customer responsive, with formulation
chemists
and
extensive
analytical
laboratory capabilities. The formulations
are validated in the real world by real-life
application testing.
Saco AEI Polymers – UK
Website
:
www.sacoaei.comSAMP
Stand: 09C60
It will be celebrations all round as
Sampsistemi celebrates its 80
th
anniversary
at wire 2016.
A number of innovative solutions for the
manufacturing of wire and cable will be on
display to highlight the importance of this
anniversary.
Aluminium and its alloys are playing an
important role in the development of
wire and cable solutions for automotive
applications, as a consequence of new
environmental regulations, price pressure
and more on-board applications.
For these reasons, Sampsistemi has
developed a whole range of products
speci cally designed for the multi-wire
drawing, in-line annealing, spooling and
successive bunching of aluminium wire.
The Sampsistemi Multi-wire Drawing
Platform (DM Platform) is based on the
splitting of gear transmission into two or
more independent sections, with separate
AC servomotors.
This allows slip recovery between each
section and at the inlet side. All motors
are synchronised by means of a control
motion system.
➣➢➣
▲
New technological developments from Rosendahl
and Nextrom