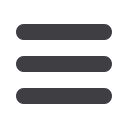

J
anuary
2012
103
›
B
ending
From tube to isometry and vice versa
OBJECT tubing is a frequent application
in the shipbuilding industry in general and
especially in hydraulics tubing. However, it
is a fact that economic efficiency falls by the
wayside if tubes are made-up at the object,
manually drawn, bent on manual bending
machines and built in, because after the
bending process it is necessary to cut
excess lengths. This means a high loss of
material. Moreover, a precise documentation
is missing, the spent working time is high
and the processed tube does not always
fit. Here an advanced, economic solution
is in demand that transfluid Maschinenbau
GmbH has just designed.
“To guarantee a constant quality of the
tubing and to achieve a minimal waste
of material with shortest possible clamp
lengths and small radii it is important
to bend the tubes in a bending centre”,
explains Gerd Nöker, transfluid CEO. “This
not only provides for the ideal quality of the
tubing but also makes possible a detailed
documentation of the tube data.”
But how do these bending tube data come
to the CNC bending machine? The provider
of solutions transfluid created two different
ways to directly compile a tube isometry
that, for example, can be made available
online (via network or email) or manually
(via USB flash drive) to the bending centre
and the bending machine. Digital drawing
with t control: The easiest method is the
use of a digital drawing tablet. transfluid
makes available the appropriate programs
for creating isometry drawings with its high-
performance software “t control”, as Gerd
Nöker explains: “A customary tablet PC can
be used. Our transfluid software enables
3D drawings of the tubes by using a pen
on digital isometry paper. An operator can
measure the desired geometry directly at
the object with the drawing tablet, draw and
send it via email to the bending centre.”
Additionally, there is the possibility to equip
the drawn geometry with flanges, welded
connections or endforming. By this, not
only a simple bending geometry can be
sent to the bending centre but a completely
ready-to-install component can be pre-
finished. For an easy inspection if the drawn
geometry matches the desired component
a 3D view of the tube is available. With its
help the drawer can identify elementary
mistakes at first glance.
Flexibility and freedom with precise
measuring arm: An optional procedure
that transfluid is providing for the safe
measurement of a tube (for example, for
reproduction) is a special measuring arm
with appropriate software. transfluid uses
measuring arms equipped with absolute
rotary encoders. They are deployed at
the object or, for example, attached with
magnet feet and provide the advantage
that they do not have to be referenced.
With these measuring systems the tubes
can be acquired by simple scanning of
the cylinders between the bends or by
scanning of the geometry. The data can
be transferred into coordinates and can be
sent, for example, by email directly to the
bending centre.
For the increase of the mobility of these
devices the systems used by transfluid can
be additionally equipped with accumulators.
The measuring data are sent directly
to a notebook computer via a wireless
connection. This provides for a maximum of
mobility without annoying cables.
Efficient bending technology: transfluid
offers the complete range for tube
diameters of 4 to 275mm for the processing
of isometries to tube geometry. The CNC
controlled and also the semi-automatic tube
bending machines are able to process the
measured or drawn tube data, to perform a
bending collision test and to appropriately
collimate and bend components that
are already equipped with flanges or
transformations. By this, the provider of
solutions transfluid has designed highly
efficient options that enable a long term
economic tube bending in the ship building
industry.
transfluid Machinenbau GmbH
– Germany
Email:
info@transfluid.deWebsite:
www.transfluid.deTube bending machines from Italy
DAVI started production of bending
machines in 1966, and currently produces
over 250 machines per year at its factory in
Cesena, Italy. Its range includes machines
to create tube from plate and machines to
bend tubes.
Since 2005 the company has produced
machines using ‘roll by wire’ technology, with
the purpose of running the entire system
through digital signals instead of relays and
contacts. Digital technology allows Davi to
produce machines that are more accurate,
user-friendly, high performing and with easy
troubleshooting.
Davi plate bending machines can
produce tubes from plates with thicknesses
from 1 to over 30mm, while its tube bending
machines have the capability to bend
pipes with diameters up to 600mm (section
modulus up to 23,000cm
3
).
The rolls are mounted on large diameter
shafts, manufactured for high resistance,
that are fixed and rotate on sphere auto
aligned shaped bearings (pre-lubricated)
to obtain a high level of performance. The
rolls are elevated thanks to large hydraulic
cylinders capable of pressing the section
that is being curved with the maximum
force required according to the diameter to
be formed.
In addition, all the rolls are motorised,
ensuring an excellent transit of the profile
during the curving process. This is made
possible by three hydraulic motors coupled
to three orbital gearboxes mounted on each
roll. The coupling motor-gearbox is a direct
mechanical coupling via a high precision
splined shaft, which permits a very high
precision connection.
The main characteristics of the machines
are high curving speed for high production
units; emergency valve to hydraulically
stop the machine rotation immediately
in emergency; total overload protection;
continuous filtering system; and high quality
hydraulic component suppliers.
Davi Promau Group
– Italy
Fax: +39 0547 317850
Email:
davi-sales@davi.comWebsite:
www.davi.com