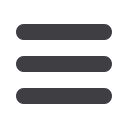

108
J
anuary
2012
www.read-tpt.com›
B
ending
All-in-one pipe bending machine
SIMAT Srl, Italy, produces special and
standard machines for tube working. The
company’s new Levitate
®
all-in-one pipe
bending machine allows the bending of
metal tubes (copper and stainless steel)
from 6 to 35mm diameter, directly from
coil. It can also make curve radius equal to
diameter.
This is made possible by a magnet inside
the machine, which makes the mandrel
(when necessary) remain in the correct
position without any external support. This
allows the user to take advantage of both
coil and mandrel working processes, without
having to use two different machines.
Levitate is versatile, and can be
integrated with other automation parts, such
as shaping machines.
The company is also working on a new
project: a special machine that will produce
serpentines with 35mm tubes and a bending
radius equal to the tube diameter.
SIMAT machines are strictly controlled
before being sold, and they adhere to all
official standards and rules. Installation and
testing take place directly at the customer’s
location by SIMAT technicians in order to
avoid lost time and other inconveniences.
Operators learn how to use the machine
directly from the SIMAT technicians,
who also provide online and just-in-time
assistance.
Levitate will be presented at Tube
Düsseldorf in March.
SIMAT Srl
– Italy
Fax: +39 0432 948882
Email:
sales@simatautomation.comWebsite:
www.simatautomation.comSwaging systems and tooling
HYDROPRO Inc, USA, manufactures
systems and tooling for hydro-forming or
swaging. The company’s equipment can full
depth expand a 400mm (15.75") expansion
zone in just a few more seconds than it
takes to expand a 40mm (1.57") zone.
The expansion pressure and dwell
times can be precisely set and controlled
to accommodate different tube material
characteristics, which is of particular use
when using tubes with high spring-back
properties such as titanium and super
duplex stainless steel.
HydroPro’s SleevePro system uses
hydroexpanding technology to expand
sleeves or liners inside damaged parent
tubes, to repair cracks or strengthen eroded
or corroded tubes. The BoilerPro system
mechanically sets and flares the ends of
boiler tubes prior to hydroexpanding or
mechanically rolling the joints.
HydroPro Inc
– USA
Website:
www.hpro.comSystem with three CNC controls
THE FL 600 3D from Tube Tech Machinery
Srl, Italy, was designed for machining tubes
and structural profiles with a maximum
external diameter of 610mm and a maximum
length of 24,000mm.
The tri-dimensional system allows
operation on any point in a sphere space,
while movement along five interpolated
axes, with precision ball screws and
linear motors, ensures high dynamics and
performance.
FL 600 3D is equipped with a double
tube loading system: one from bundle,
which allows the automatic loading of
tubes with round, square and rectangular
section and a loading capacity of 10,000kg,
and one from chain, which also enables
the loading of open section profiles. It
is composed of V-shaped supports: the
chains move at variable speed, according
to the tube diameter and weight, and are
made to slide on bearings to prevent noise
and wear. The movements of the piece
along the working axis are ensured by
four self-centring mandrels, activated by
synchronised hydraulic cylinders.
A tempered and rectified precision helical
toothed rack activates the advance, operated
by brushless motor and precision reducer
with slack recovery system. The mandrels
are designed to allow the machining
of different diameters and sections,
with no change of tools. An integrated
floating system allows the compensation
for a piece’s uneven straightness during
machining, enabling precision machining
even on particularly irregular tubes, and
preventing dangerous mechanical stress
on the mandrels. The plant is automatically
controlled by two CNC controls: one for
the handling area and the other for the
laser working area (Sphera). A third CNC
control manages and supervises the laser
source. The three computers are set to
interact with one another, with no need
for human operation: they automatically
handle profile loading, dimensional control,
3D laser machining and discharge of the
machined parts.
The software is simple and user-friendly,
and can be upgraded to include the handling
of lists of materials and stock.
Tube Tech Machinery Srl
– Italy
Fax: +39 030 7256333
Email:
info@tubetechmachinery.comWebsite:
www.tubetechmachinery.comLevitate all-in-one pipe bending machine from SIMAT