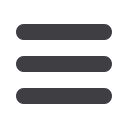

J
anuary
2012
105
›
B
ending
Simulation module
facilitates correction of
bending machines
WITH the launch of software version
4.7, AICON’s TubeInspect optical tube
measuring system allows the operator to
simulate the bending process considering
individual correction values, and to verify
their effect on accuracy to gauge by means
of a virtual gauge check.
With the help of high resolution digital
cameras, TubeInspect determines the
tube geometry within seconds, and proves
accuracy to gauge. The system shows in
detail which bending points deviate from
the desired values, and suggests correction
values. These correction values can be
transmitted directly to the bending machine,
whereby TubeInspect allows the connection
to up to 100 benders.
In some instances the correction values
suggested by TubeInspect cannot be
transferred one-to-one, for example if they
lead to collisions at the bending machine or
if corrections are suggested at parts which
cannot be affected because of solid bending
tools. This is where the new simulation
module is of benefit: when TubeInspect
evaluates a measured tube as a bad part
and suggests correction values, the operator
can adapt them at his own discretion, as
he knows the actual circumstances and
characteristics of his bending machine.
By doing so, the operator does not take
any risk, because TubeInspect simulates
the results of the changes and shows with a
virtual gauge check if the bending process
could actually produce a good part. When
the right settings are found, another real
bending test will take place. This results in
fewer bending tests being necessary, which
makes the setup process even leaner.
AICON 3D Systems GmbH
– Germany
Fax: +49 5 3158 00060
Email:
info@aicon.deWebsite:
www.aicon3d.deThe virtual gauge inspection confirms a successful
correction and the production of a good part
Virtual gauge inspection reveals a bad part
The TubeInspect optical measuring system measures
tube geometries using high resolution digital cameras
End forming/roll forming machine
MANCHESTER Tool & Die Inc offers the
hydraulically operated Model M10-H-
3-R End Forming/Roll Forming Machine,
featuring standard MTD components and
using the same tooling as the M71-H-
3 and 24008 machines. The M10-H-3-R
offers the HMI (Human Machine Interface)
user-friendly, programmable flexible
control system and includes diagnostics
for machine maintenance. The end forming
and roll forming stations are positioned
so the operator can load and unload both
clamp areas.
A design offering future auto loading
and unloading systems allows tube end
forms requiring end forming and roll forming
processes to be completed without any
staging of materials between processes.
The M10 can also be designed with a
6-position end form station for tube end
forms that require components to be
assembled onto the tube before the rolling
processes. The machine footprint is 72"
wide x 96" deep.
Manchester Tool & Die Inc
– USA
Email:
testeffen@mtdtube.comWebsite:
www.manchestertoolanddie.comThe Model M10-H-3-R end forming machine