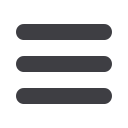

Technology News
www.read-tpt.comS
eptember
2013
49
Compact measurement system
for single layer products
CUSTOMERS that buy an X-ray
instrument from Sikora expect an
improvement in production processes
and simple handling as well as the
simple integration of the new product
into the production line. To meet these
needs, the engineers at Sikora designed
the X-RAY 6035 to be even more
compact.
“Saving space is a critical aspect during
the integration of a new device,” said
Harry Prunk, CEO of Sikora AG. “If the
line has to be rebuilt it can be expensive.”
Sikora
provides
two
X-ray
measurement systems for quality
control during the hose and tube
extrusion process: the X-RAY 6000
and the PRO version. The X-RAY
6035 is specially designed for product
lines where only one layer of material
or the total wall thickness is measured.
It is a cost-effective yet highly powerful
instrument for continuous measurement
of inner and outer diameter, wall
thickness and eccentricity of single
layer tubes and hoses. Besides various
products made of PE, HDPE, PVC
and EPR, foamed pipes and hoses of
EDPM, nylon, rubber or silicon can also
be measured reliably.
With the X-RAY 6035, the engineers
at Sikora have succeeded in reducing
the dimensions by 20 per cent –
which not only saves space but also
resources.
In the ongoing process the product
is X-rayed while the data of the high-
resolution CCD sensors provides the
basis for preparation of the measured
values in a split second. The production
data is displayed on a 7" monitor
with touch screen operation that is
integrated directly into the measuring
system – at a glance, the operator
has all the data required for accurate
centring of the crosshead. The optional
combination with the processor system
ECOCONTROL 600, 1000 or 2000
enables the automatic and reliable
control of the extruder speed or line
speed, taking account of the minimum
values.
This technique has a great advantage
over alternative technologies – the
X-RAY 6035 requires no calibration.
“The device works regardless of
the ambient conditions, such as the
temperature of the product to be
measured,” said Mr Prunk.
The X-RAY 6035 is available for
single layer products with a diameter
of 5 to 30mm. For multilayer pipes
and hoses, Sikora offers the X-RAY
6000 PRO. Ranges up to 650mm are
available on request.
Sikora AG
– Germany
Email:
sales@sikora.netWebsite:
www.sikora.net For ‘starter’ tube hollows that lead to a perfect finish … ...trust Tube Hollows InTernaTIonal: the world leader in seamless precision. To achieve seamless perfection in your drawn and reduced finished tubes, you need ‘starter’ (or ‘mother’) tube hollows with extreme uniformity of wall thickness and consistent concentricity. And that means your search begins and ends at Tube Hollows International . We can meet your specs precisely for deep hole drilling, trepanning, honing, grinding and finished part machining … working with all commercial and medical grade alloys— stainless, titanium and carbon steels …for a range of demanding industries— aerospace, medical and energy . Contact Evan Spoerl to discuss your needs or get a free quote, today: 207.892.2352 or espoerl@tubehollows.com 39 Enterprise Drive #2, Windham, ME 04062 USA • T 1.207.892.8899 • F 1.207.892.8863 • TubeHollows.comTube
bending
YORKSHIRE,
UK-based
Olicana
Products Ltd, a tube bending specialist,
has recently completed the production
of its five millionth tubular steel bath
leg using an unmanned robotised
manufacturing cell supplied by Unison
Ltd. Olicana purchased the automated
5-axis tube bending cell eight years ago.
The process includes automated
loading of the cut lengths of tube into the
automated 5-axis tube bending machine,
and robot removal and placing of the
complex bent tube into an all-electric
press that punches holes into the product
in different planes. A robot then moves
the finished product from the press and
places it onto the collection rails ready for
packing and distribution.
Olicana’s managing director, Rupert
Pearson, attended Unison’s 40
th
anniversary dinner and official opening
of its new manufacturing facility in June.
Olicana Products Ltd
– UK
Fax: +44 1943 816298
Website:
www.olicana.com