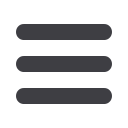

March 2015
Cement & Concrete
T
hecompany’sGroupConcrete&
ResearchManager, Cyril Attwell
says, “We have been able to
carry out an enormous amount of
testing on these slabs. The latest
strengths achieved are 75 MPa to
85 MPa after about nine to 12months
since installation. Essentially what
we are doing is conducting trials for
future applications of geopolymer
concrete.”
Characteristics being investigated
include durability and abrasion resis-
tance. “The abrasion resistance is far
higher than that of normal concrete
because it does not use water as its
critical mass.” Attwell explains that
geopolymer concrete refers to alkali-
activated material. “The production
of geopolymer concrete in civil con-
struction projects is fairly recent.”
Murray & Roberts is also looking at
the application of geopolymer con-
The Murray & Roberts Group is pioneering the latest
developments in concrete technology in its ongoing effort to
become a carbon neutral construction company. Research
initiatives in this regard include the long-term testing of
geopolymer concrete at Transnet’s City Deep Container
Terminal in Johannesburg, a contract undertaken by Murray
& Roberts Infrastructure for client Transnet Capital Projects.
crete in mine infrastructure, with a
current trial taking place at the Matla
Brine Ponds project.
“Infrastructure is a major focus
as this needs concrete that is highly
durable and versatile. However, one
of the biggest potential applications
of geopolymer concrete is for the
control of nuclear radiation.”
Attwell points to research conduct-
ed at the University of Sheffield in the
UK, whereby geopolymer concrete
was used to effectively neutralise the
highly radioactive casings of nuclear
fuel rods by essentially binding the
radioactive substances within the
concrete material itself. This renders
geopolymer concrete highly suitable
for South Africa’s estimated R1 trillion
nuclear-build programme.
Another sustainability feature of
the City Deep project was Transnet
Capital Projects’ stipulation that the
company had to recycle the old con-
crete from the site. About 86% of the
old worn concrete pavements were
broken up and reused, amounting to
123 840 m
3
of the total 144 000 m
3
of
concrete. This far exceeded the cli-
ent’s original requirement.
“Transnet is a forward-thinking cli-
ent, as shown by the fact that wewere
able to install geopolymer test slabs.
Due to the success of the project,
the client is now excited about the
process going forward, as it is looking
actively at other projects where the
use of concrete is limited.”
A particular environmental benefit
of geopolymer concrete is that it does
not require water for the curing pro-
cess. “Water is a scarce resource, and
its use is likely to become very con-
strained in the construction industry
in the near future. We are currently
designing a geopolymer concrete
that can be cured by utilising carbon
dioxide, with the added benefit of
this material acting as a carbon sink
as it traps the carbon dioxide in the
geopolymeric form. This means the
concrete becomes much stronger far
more quickly,” says Attwell.
Other research initiatives include
the development of a ‘coral concrete’
for marine environments. “We are
looking at applying an electro chemi-
cal process to our marine concrete
Concrete strives for