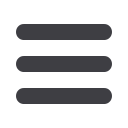

T
he Ukrainian company opted
for a customised tailor made
solution fromweiler. A team of
engineers from weiler designed and
installed the new weiler Multi-caster
line into a 24 x 100 m of floor space.
The production line consists of six
steel casting beds, each 96 m long,
foundation piles and lintels are being
slip-formed continuously, using the
new weiler Multi-caster with three
quick-exchange cartridges.
After only eight hours curing time
the products are cut to the required
lengths with a high performingweiler
concrete saw. After lifting of the cut
elements, the production beds are
cleaned with an LPG motor driven
weiler ‘weasel’ – this machine also
sprays demoulding oil and pulls pre-
stressing wire.
KHM required a daily capacity of
1 000 linear metres of foundations
with cross sections of 30 x 30 and 35
x 35 cm lengths of up to 18m. Produc-
tion targets surpassed expectations
and KHM took over the plant, ready
for operation.
Today, with only eight operators
up to 1 700 linear metres of founda-
tion piles are being produced in a
single shift operation.
Shorter curing times, significant
material savings, substantially higher
performing final product, reduced
steel content, minimised the quantity
of cement – approximately 200 kg ce-
ment less per m³ of concrete, which
meant a saving of €2 500 per day.
“The newproduction line is paying
off,” said KHM’s Production Chief.
■
weiler’s slip former plant for
prestressed foundation piles
Khmelnizkzalisobeton (KHM), a Ukrainian construction company,
produces hollow core slabs using a Finnish extruder production
line and reinforced foundation piles made of wet-cast concrete in
molds. To meet the increased demand for 4 000 foundation piles
required for each project, the existing production method could no
longer meet the requirements for high capacity production while
respecting design tolerances.