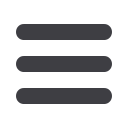

32
CONSTRUCTION WORLD
MAY
2016
PROJECT PROFILE
>
Following the completion of
another civil engineering construc-
tion contract at the iron ore mine
later this year, the leading South
African infrastructure specialist, which forms
part of Murray & Roberts Construction, will be
establishing itself elsewhere in the country to
start working on a road construction contract
for a major local roads agency.
Murray & Roberts Infrastructure recently
completed the civils works for the mine’s new
Heavy Mining Equipment filling station and
storage tank area. This infrastructure will be
used to service the giant Komatsu rigid dump
trucks that haul iron ore out of the pit to the
tipping point.
Murray & Roberts Infrastructure’s
contracts manager, Tiaan Krugel, says one
of the complexities of this project was the
number of working faces on the contract
and the extremely fast track nature of the
project, which was completed in as little as
six months.
“The biggest challenge we faced on this
contract was the number of working faces from
day one. There were at least 10 at any given
time during the project duration,” he says.
Coping with the formidable task at
hand called for excellent team work, and
Krugel notes that the client’s involvement
helped tremendously.
“The client did a great job in terms of
managing the project. It was extremely proac-
tive, which helped us moving forward.”
The contracting team also had to take a
proactive approach to managing the arrival
of a host of built-in and cast-in items for the
project. While lead times for some items, such
as the pipelines, are 12 weeks, he says that
the biggest hurdles occur before the actual
order is placed with the vendors. All docu-
mentation can take up to 18 weeks to finalise
to receive the necessary permission to have
the items delivered to site.
“Sometimes, it can take between three
and four months before you get everything
to site, so you have to plan very carefully”
says Krugel.
Big pours
One of the highlights of the build was the
600 mm concrete slab that makes up the
forecourt of the filling station. Constructing
the 90 metre by 66 metre forecourt called for
the placement of 4 800 m
3
of concrete – with
a total of 8 000 m
3
poured – and 570 tons of
reinforcing bar – with a total of 770 tons for
the entire project.
Between six and eight readymix trucks
ran to and from the batching site a day.
The sheer number of trucks was necessary
considering that 3Q Concrete’s batching plant
is located eight kilometres from the site.
A total of 18 pours were needed to
complete this aspect of the works with the
HME FILLING STATION
at Sishen
Work may have been undertaken outside the
so-called ‘red zone’ at Sishen mine in the
Northern Cape, but this did not make one of the
last contracts Murray & Roberts Infrastructure
undertook for Kumba any easier.