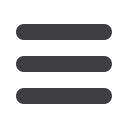

34
CONSTRUCTION WORLD
OCTOBER
2016
ROADS AND BRIDGES
This has certainly been the case
on the upgrade of the stretch of
the National Route 1 (N1) from
Sydenham (km 28,8) to Glen Lyon
(km 62,4). Once completed, the project will
again highlight South African road construc-
tion capabilities and, just as importantly,
showcase the capabilities housed in the
Raubex Group.
The road will have an extremely high
rideability specification, as well as a life-
span of approximately 20 years, in line
with consulting engineer, WorleyParsons’
design requirements.
Contracted by the South African National
Roads Agency SOC Limited (SANRAL), Raubex
Construction and sister company, Roadmac
Surfacing are making steady progress on this
construction programme.
The road comprises 350 mm of G4 stabi-
lised sub base, 120 mm of bitumen treated
base (BTB) course and 20 mm of ultra-thin
friction course (UTFC).
Raubex is tasked with constructing the
sub-base layers while Roadmac Surfacing
oversees the BTB and UTFC components of
the upgrade.
Despite a few complexities, the consor-
tium of Raubex companies is planning to
hand over this project well ahead of its
completion deadline in December 2016. This
follows almost 18 months of building activi-
ties on this important national road artery.
Reasons for solid track record
Wimpie Koch, contracts manager of Roadmac
Surfacing, attributes the sound track record
of the company to a number of factors.
Firstly, the company made a solid start
right from the outset. When Raubex started
with its component of the works, Roadmac
Surfacing immediately commenced with the
design of the asphalt.
At the same Petra Quarries, owned
and operated by Raumix Aggregates, and
B&E International started producing and
stockpiling the 26 mm BTB aggregate needed
for the base layer, while National Asphalt
commenced crushing the high specification
UTFC aggregate required for the contract.
These companies are part of Raumix,
the materials division of the Raubex Group,
and they were also joined by sister company,
Tosas, which supplied the bitumen emulsions.
Recycled asphalt
Koch tells
Construction World
that the asphalt
mix design comprises a high percentage of
recycled asphalt (RA) – in line with govern-
ment’s ‘green’ infrastructure movement.
Initially, the professional team believed
that it would be able to exceed these
requirements and, with input from Roadmac
Surfacing, the BTB asphalt supplier bought a
state-of-the-art batching plant that is able to
produce asphalt containing a 40% RA.
As much as 5 000 tons of asphalt
comprising this high percentage of recy-
cled pavement was placed in the very early
stages of the contract. However, the quality
of material recovered in the fast lanes of the
N1 highway was insufficient and Roadmac
Surfacing decided to lower the percentage of
RA used in the asphalt mix.
Despite this, Roadmac Surfacing has
exceeded SANRAL’s expectations. “At present,
we are placing an asphalt mix with a 30% RA
component, which is significantly more than
our client expected,” says Koch.
“While introducing a second team to
undertake asphalt batching activities at the
batching plant may have come at an extra
cost, the time savings were well worth it. We
were able to gain at least a six week head
start on this project by implementing these
interventions,” he says.
Koch says the biggest challenge on this
project was the smoothing over of produc-
tion challenges at the new plant. This was
essential, considering that asphalt produc-
tion is on the critical path of the
entire contract.
SMOOTH OPERATOR
on N1 upgrade
The Raubex name is
synonymous with quality
road infrastructure.
It therefore stands to
reason that member
companies of the largest
road building specialist
in the country will strive
to exceed expectations in
the immediate vicinity of
its own headquarters in
Bloemfontein, Free State.
>
Asphalt is batched in a state-of-the-art plant that is able to produce asphalt with a RA content.
“The accuracy of the final
layer of the BTB is critical,
as it will influence the layer
of UTFC that is placed on
top of it, and if not 100%
could compromise the high
rideability specification
demanded by SANRAL.”