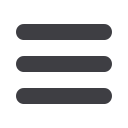

May 2015
71
wire Russia – Krasnaya Presnya Expo fairgrounds, Moscow, Russia 12
th
-15
th
May 2015
wire Russia 2015
Mikronix uses a developed powder
coating technology. By developing new
techniques in the eld of electrostatic
and lter systems it has succeeded in
simplifying the machine, reducing the
consumption
considerably,
reducing
costs, but maintaining the powdering
quality.
Mikronmakina Electrostatic Powder
Machines Co – Turkey
Website
:
www.mikronixcable.comMaschinenfabrik
Niehoff
Stand FOD44
At this year’s wire Russia, Maschinenfabrik
Nieho and Nieho of Russia are showing
the following exhibits:
•
an MSM 224 type wire-drawing
machine for intermediate wire range
with RI 250 type continuous inductive
inline annealer
•
a D 632 double-twist bunching
machine with ARP 630.1 pay-o
The electronically driven MSM 224 wire-
drawing machine for the intermediate
wire range with continuous inductive
inline annealer type RI 250 is preferably
used for wires made of copper alloys such
as brass, bronze and German silver.
Nickel and nickel alloy wires as well as
other non-ferrous metals like platinum,
rhodium and special materials can also be
produced.
The machine is capable of drawing wires
with a maximum inlet diameter of 3.7mm
to a nal diameter range of 0.2 to 1.8mm
(depending on the material).
Other features include a completely
submerged drawing process and die
holders with high-pressure lubrication. The
drawing capstans are made from a cera-
mic composite material and individually
driven by water-cooled AC motors.
This drive principle enables a minimised
slip operation resulting in wire with a
very high surface quality and minimised
energy consumption.
With help of the single drives the wire
elongation
between
the
di erent
drawing capstans can be varied over
a wide range. In this way, for di erent
alloys, in each case the optimum wire
elongation can be adjusted.
The continuous inductive inline annealer
type RI 250 is, like the other models of the
RI series, built in several sizes designed
for wires with low electric and thermal
conductivity.
RI type annealers work on the principle
of an excitation voltage transformer.
This principle and the fast cooling of the
wire enable a ne-grained structure,
giving the wire excellent processing and
forming properties while ensuring a high
wire surface quality.
The D 632 type double-twist bunching
machine is designed for strands with 0.09
to 6mm² cross section and a steplessly
variable lay length of 6 to 100mm. The
maximum number of twists is 6,500
twists/min, the maximum speed 300m/
min.
Other features of the machine include
the service proven energy-saving single
bow (ECO-Bow) design, the contactless
transmission of machine data within
the machine and a sophisticated drive
concept. Compared to conventional
bunching machines, energy consum-
ption and noise emission are signi cantly
reduced due to the one-bow design.
The relatively small rotor driving motor of
energy e ciency class IE3 is characterised
by a high degree of e ciency, and
reduces power consumption. The 230V
voltage supply in the spool carrier leads
to an increased transmission security
at the slip rings, and three-channel
telemetry enables an absolutely secure
signal feedback and a greater control
accuracy of the lay length. The drive
concept results in robust operation, free
of dancer or spooler vibrations.
Operation is carried out via a panel with
a 10" touch-screen display with with
a new colour user interface: the NMI
(Nieho Machine Interface) with a clear
navigation structure according to a
uni ed concept.
➢➣➢
▲
Electrostatic
powder
application
from
Mikronmakina
▲
The MSM 224 type wire-drawing machine from
Nieho