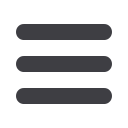

T
ube
B
ending,
H
ydroforming &
E
nd-
Fo
rming
116
M
ay
/J
une
2007
Presses and tooling alone do not satisfy
the increasing demand for hydroformed
components
in
today’s
automotive
manufacturing industry.
Prior to downstream processing, nearly
every hydroformed component requires
critical preliminary or secondary operations
such as pre-bending, trimming, shearing,
end-forming, piercing, poke yoke inspection
and palletizing.
Wayne Trail Technologies, USA, provides
innovative equipment and automation
solutions to help complete the tubular
hydroform process. The company offers a
tubular hydroform solution from stand-alone
machines to turnkey system integration and
overall line control.
The company supplies to a variety of
market segments, including metal stamping
and forming, tube bending and fabricating,
robotics, welding and fixturing, and laser
welding and cutting systems.
Wayne Trail Technologies
– USA
Fax
: +1 937 295 2642
:
info@waynetrail.comWebsite
:
www.waynetrail.comForming both ends of the
exhaust market
Ava-Matic, UK, has been manufacturing
its range of tube end-forming machines
for over 20 years. This range is supplied
for applications including exhausts, for
both ends of the spectrum from mass
production to the bespoke requirements
of many Formula 1 teams. The company
has recently received an order for
eight machines from a large European
manufacturer.
The footprint is extremely compact on both
Ava-Matic’s single and twin head machines,
meaning that the design is especially
suitable to form part of a production cell.
With a capacity for up to 160mm diameter
tube, the machines have extreme efficiency
for their size. These features have made
the machines ideal for use in all types of
applications including the furniture, dairy/
brewery and tube fitting industry.
The machine includes a semi-automatic
mode that allows the operator to expand or
reduce the tube in a series of steps (pulses)
to reduce splitting and maintain consistent
close tolerance accuracy. All controls have
been designed for ease-of-use and rapid
setup, with completion of tool changeover
in less than a minute.
Ava-Matic
– UK
Fax
: +44 1527 518526
:
info@avamatic.co.ukWebsite
:
www.avamatic.co.ukCritical manufacturing of hydroformed components
fi
A hydroformed tube being loaded over a mandrel
in a tool that will pierce a radius for later use to
weld the bushing at the end of the part. Following
punching, the part is driven off of the mandrel
and slugs and scrap are shed into
a collection
system