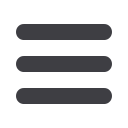

112
M
ay
/J
une
2007
Bending sleeves are cut to size and
placed into the tube assembly along with
grounding spacers using a proprietary set-
up method. Following the bending process,
tubes are visually inspected for defects.
They are then degreased and cleaned, the
inner tube ends are trimmed to length and
fittings are installed.
Results with Wolfbend are much more
consistent than for hot wax and scrap
rates are closer to single wall tubing,
primarily because the physical
characteristics of the bending
sleeve are better suited to
the purpose. The sleeve is a
proprietary Teflon formulation
that is very good in compression
and also stretches and cold flows
well in tension.
Combined with the self lubricating
properties of Teflon, this leads
to good tube wall flow and
consistent bend support. Typical
design gap is
1
/
8
", ie a 1.00 OD
inner tube requires a 1.25 OD
outer, and smaller gaps can
also be bent. Bend defects such
as wrinkles and ovality tend to
mirror between tubes, simplifying
inspection and eliminating the need for
X-ray. The processing time for Wolfbend is
typically a few hours.
Aero Arc Inc, USA, manufactures double
wall tubing for the Boeing 717 and
C17 using the hot wax process and for
Bombardier Regional Jets using Wolfbend.
Mr Rick Rohrberg, vice president of
Engineering at Aero Arc, says,
“The
Wolfbend bending sleeve is much better
than hot wax because it’s fast, easy to
use, and works well. The phenolic spacers
used with hot wax are only in straight
sections and fit loosely which can allow the
tubes to resonate. The Wolfbend sleeve
is secured tightly by bending and gives
support in the bends where it’s needed.
The Wolfbend™ grounding spacers are
also a great feature. The hot wax method
requires the tubes to be independently
grounded with straps at installation. With
Wolfbend the grounding is incorporated
and it really simplifies things.”
Aero Arc Inc, based in California, is an
aerospace
component
manufacturer
specialising in tube bending, sheet metal,
machining, and welding since 1982. Aero
Arc also manufactures PMA licensed
tube and duct assemblies for MD/Boeing
aircraft.
Wolfbend™ was developed for aircraft
fuel lines but it has already found
new applications meeting SFAR 88
safety requirements for wiring conduits
in fuel tanks. Its design, safety and
manufacturing
advancements
may
find application outside aerospace in
industries such as petrochemical and
pharmaceutical process piping, heat
exchangers, and submarine and ship
systems.
Davis Aircraft Products Co Inc is the
exclusive Wolfbend marketing licensee
and it is currently used under sublicense
by Bombardier, Cessna, Mitsubishi
Heavy Industries, Aerospace Industrial
Development
Corporation
(Taiwan),
Aero Arc (Torrance, California), BHW
Components Ltd (Lancashire, UK), GE
Elano Canada, and OSM Partners LLC
(Savannah, Georgia).
This article was supplied by Mr Rick Rohrberg, vice
president of Engineering at Aero Arc Inc, and Mr Larry
Wolf, president of Wolfbend LLC.
Davis Aircraft Products Co Inc
– USA
Fax
: +1 631 563 1117
:
ddavis@davisaircraftproducts.comAero Arc Inc
– USA
Fax
: +1 310 381 0173
Website
:
www.aeroarc.com›
Wolfbend technology uses a bending sleeve that fills the gap
between tubes but remains in place after bending
The sleeve is a
proprietary Teflon
formulation that is
very good in
compression and
also stretches and
cold flows well
in tension
❱
❱
88
T
ube
B
ending,
H
ydroforming &
E
nd-
Fo
rming