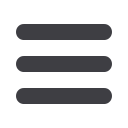

T
ube
B
ending,
H
ydroforming &
E
nd-
Fo
rming
107
M
ay
/J
une
2007
reliability and cycle time. The company’s
range of all electric benders have been
designed according to essential criteria
including high efficiency, clearance and
robustness.
Using the machine, the mechanical
ball screw designs used for the slides
can be synchronised via the flexible
EPT BendPro G2 control. Slide motions
can therefore be overlapped to further
minimize cycle time.
Eagle Precision
recently
received
reports from a hydroforming
parts supplier using an all-
electric Eagle bending machine,
model EPT90EPS (3.5" OD capacity). The
parts supplier revealed a cycle time of 19
seconds for a 3.25" OD X 0.070" wall X
5"CLR 5 bent part. This statistic equates to
4 seconds per bend compared to 5 seconds
per bend as seen on competing hydraulic or
hybrid products.
With 35 years of experience, Eagle
Precision Technologies is a world leader in
the manufacturing of CNC tube benders,
tube end-finishing equipment, custom
machine building, muffler manufacturing
equipment and tooling.
Eagle Precision Technologies
– USA
Fax
: +1 519 756 0195
:
jwarren@eaglelept.comWebsite
:
www.eaglept.comSoco’s latest machine with 1D
bending and thickness control
A new model of CNC tube bender has been
launched by Soco, branded the SB-65X6A-
3S-PT with cutoff, which incorporates the
ultimate combination of automation and
high production features in one package.
It offers advantages including 1D bending
and thickness control.
This machine includes 8 electric
programmable axes, coupled with a unique,
patented Soco DBS system. Designed for
minimal tube deformation after bending,
the DBS system provides double blade
shearing and vertical/horizontal cutting.
Features include a centreline radius (CLR)
of 1 X OD bending in stainless. With 12 to
15 per cent wall thinning ratios (WTR), the
machine can help meet the strictest safety
demands of muffler and exhaust system
suppliers. A cutoff during and after bending,
together with continuous bending from one
long part, ensures no waste between parts.
A special collet boosting device is
included to allow 1D and low WTR even
for short lengths and last bends. In
addition, multi stacks and multi radius
is available for bending even the most
complex parts with ‘0’ straight lengths
between bends.
Soco Machinery Co Ltd
– Taiwan
Fax
: +886 4 23592386
:
patrick@soco.com.twWebsite
:
www.soco.com.twHydroforming is a cost-effective way of
shaping malleable metals such as steel
into lightweight, structurally stiff and strong
parts by injecting fluid at high pressures
into a tube to form the material into a die
cavity. One of the largest hydroforming
applications is in the automotive industry
where producing a consistent part shape to
the hydroforming die is essential.
The first step in producing hydroformed
shapes is bending a tube to a net shape
to fit the die prior to hydroforming. This
step of the process requires exact bending
procedures
and
accurate
machine
operation to minimize scrap and fit the die
correctly.
Any variations in the bent part
shape may produce part
pinching in the die and
subsequently scrap. In
addition to the accuracy
requirements
of
the
hydroforming
procedure,
the bending machine cycle time
must be minimized.
Traditional hydraulic or hybrid
(electric and hydraulic) benders
can produce bent tubes to fit
dies. However, any axis that
is hydraulically actuated may
experience process variation
until hydraulic oil temperatures
stabilise. In addition, the actuators on
hydraulic or hybrid benders are typically
only two-position and therefore cycle times
cannot be minimized.
Eagle Precision Technologies Ltd has
introduced a family of all electric benders
that addresses the specific needs of the
hydroforming world. These concerns
are essentially high-speed, accuracy,
Hydroforming and the all-electric tube bender
fi
An all electric bender from Eagle Precision Technologies
fi
The automotive industry requires consistent part
shape for hydroformed products
›
Soco’s new CNC tube bender – SB-65X6A-3S-
PT with cutoff